高洗浄パージ剤が黒点不良を防ぎ、
品質改善に貢献します!
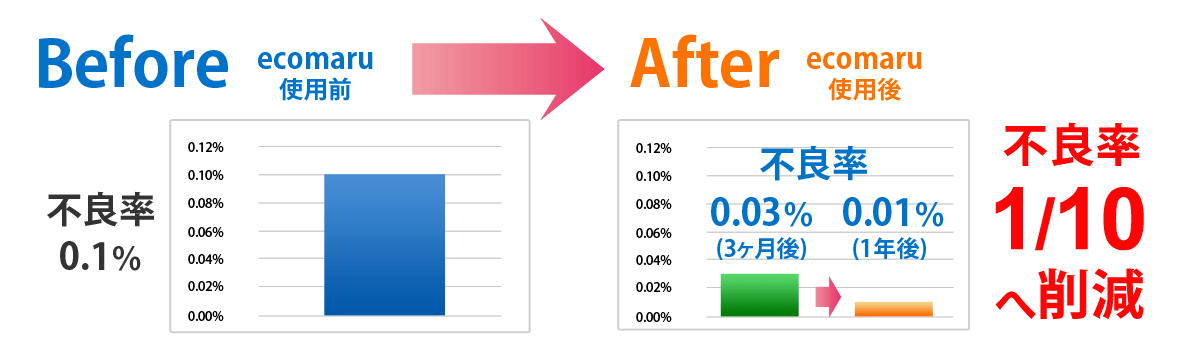
ecomaruは射出成形機のシリンダー内部洗浄専用のパージ剤です。GW(グラスウール)を高配合し、黒点除去性能を最重視。GF(ガラスファイバー)では落としきれなかったシリンダー内の樹脂劣化物(焼け・黒点)を除去・予防し、黒点不良など異物不良率の低減、品質改善に貢献します。
パージ剤とは?
パージ剤とは、射出成形機用洗浄剤とも呼ばれ、色替え、樹脂替え、外観不良率の低減、異物発生を予防するために用いられる洗浄剤ペレットです。射出成形機における「洗浄」とは、シリンダー内に残った成形材料や焼けた炭化物、汚れを排出することです。パージ剤には、ガラスフィラー入り、界面活性タイプ、発泡タイプ等があり、用途に応じて使い分けられます。
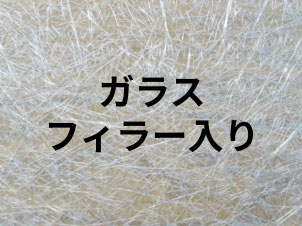
ガラスフィラー入りパージ剤
ガラス繊維を含むパージ剤で、強力な摩擦力で洗浄します。スクリュー、シリンダーにこびりついた炭化物の洗浄に適しています。
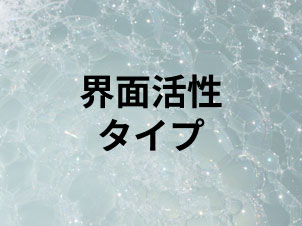
界面活性タイプ パージ剤
界面活性剤が含まれたパージ剤は、前材(後材)と金属表面の間の界面張力を制御して排出性を高めます。
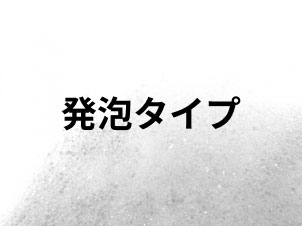
発泡タイプ パージ剤
発泡性のある樹脂で、スクリュー壁面のこびりつきを除去しながら押し出すのが発泡タイプのパージ剤です。
世界初!GW(綿ガラス繊維)を使用したパージ剤
ガラスフィラー入り洗浄剤(パージ剤)で使用されているガラス繊維は、一般的にはGF(ガラスファイバー)です。ecomaruはGFよりも繊維が細かいGW(グラスウール)を使用し、さらに高洗浄を実現。グラスウールは繊維長が短く、繊維径は細く柔らかいため、無数のガラス繊維角と圧倒的な比表面積で効果的に不要物を削ぎ落とします。
従来の洗浄剤
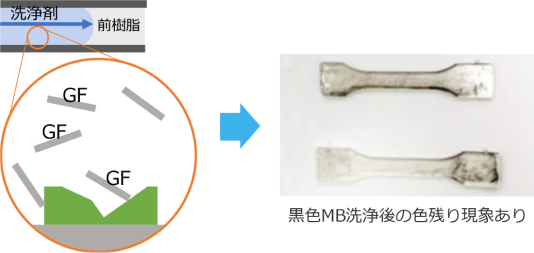
ecomaru
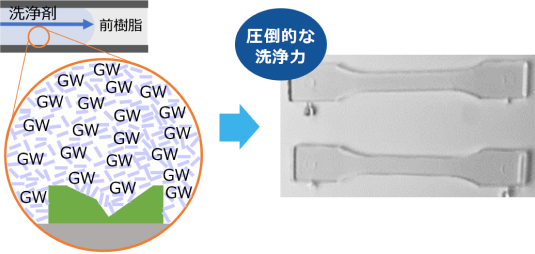
パージ剤の役割
ecomaruは特に、炭化物・黒点除去に威力を発揮する高洗浄タイプです。
- 現在ガラスファイバー入りを使っているが、パージ剤コストが高いと感じている。
- 現在ガラスファイバー入りを使っているが、ガラス残りが気になり、GF入りパージ剤で洗浄したあと、さらに通常のパージ剤で洗浄している。(すすぎ洗い、二度洗い)
- 黒点不良対策にガラスフィラー入りが良いとは聞くが、成形機を傷めないか?コストが高いのでは?と躊躇していて、発砲や界面活性タイプ、共材で置換している。
- 難燃材や塗装しない成形品の黒点不良で悩んでいる。
- 射出成形現場のQMSでさらなる品質改善を求められている。
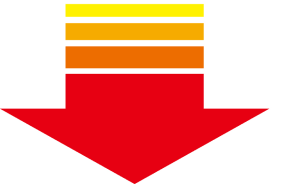
ecomaruをお試しください。
ecomaruの特徴

高洗浄パージ剤が、かつてない洗いを実現。
黒点不良を改善し、不良率低減に貢献。
大手電機メーカーの試験サンプルをご覧ください。ABS(黒)をパージした際のショットごとの洗浄比較です。5ショット目を見るとecomaruの方が濃い黒が見えています。成形機の汚れ具合にもよりますが、ecomaru内の微細なグラスウールがこれまで成形機内に蓄積された汚れを隅々まで洗浄するため、同じショット数で比較した際、他社パージ剤よりも色が濃くでることがあります。
続けて10ショット、15ショットと打ちました。ecomaruの方が早く洗浄が完了しており、15ショット目で比較すると他社パージ剤ではまだ黒いものが残って見えます。洗浄性に大きな差があることが確認できます。

新素材GWのリサイクル素材を60%使用。
環境にやさしいアップサイクル製品。
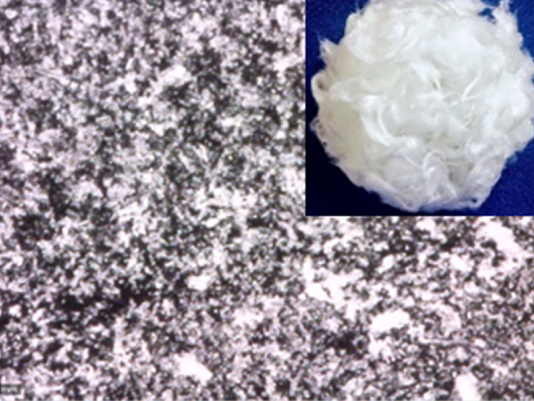
グラスウール(ガラス繊維)は、ガラスを高温で溶かし細い繊維にして綿状にしたものです。断熱性・吸音性・防振性に優れ、暑さ/寒さ、騒音、振動などを遮断するのに用いられています。
当社は断熱材となるグラスウールの端材を利用し、「グラスウールを原料としたパージ剤」を世界ではじめて開発。地球環境に優しい素材で、従来のガラスファイバー入パージ剤より高洗浄を実現しました。
SDGs対応
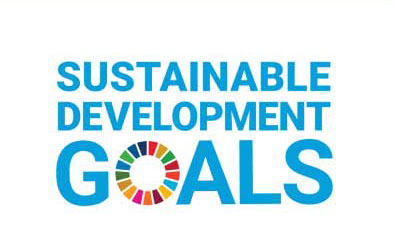
60%使用
成形機に優しい
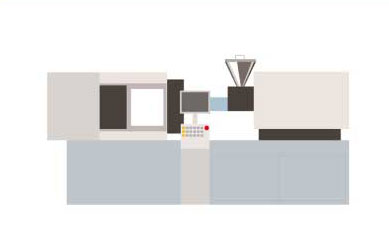
成形機に優しい
高洗浄を実現
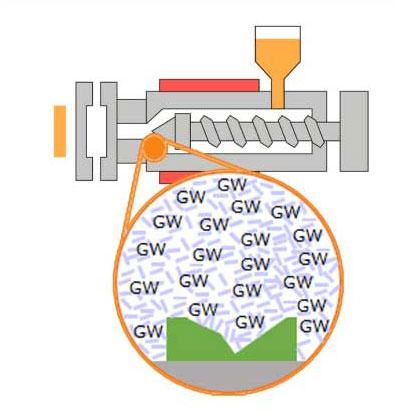

後続樹脂置換性に優れ、
「パージ剤残り」成形不良を防止。
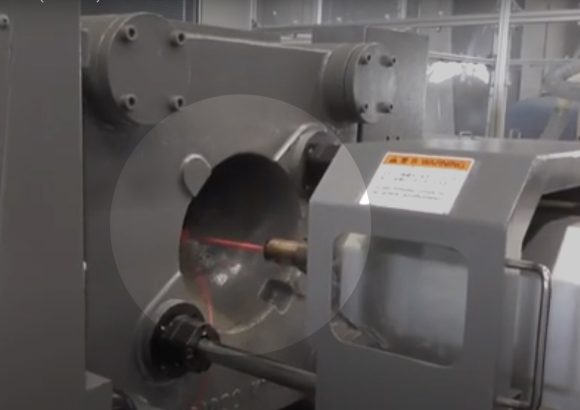
後続樹脂置換性とは、パージ剤で洗浄後、後続樹脂を入れた際、どの程度素早く確実にパージ剤を排出し、次の樹脂に切り替わるかどうかの性質です。パージ剤が高洗浄であることは重要ですが、洗浄後しっかり排出されるかどうかも非常に重要です。特にガラスフィラー入りのパージ剤はガラス残りが気になって使用することに抵抗があったり、「二度洗い」をしている成形現場も多いのではないでしょうか。パージ剤が排出されずに残ってしまうと「パージ剤残り」となり、黒点不良を防ぐはずのパージ剤が成形不良を引き起こすという本末転倒な事態を引き起こします。
ecomaruは高洗浄でありながら、優れた置換性を示すパージ剤です。検証として、赤色のABS樹脂をecomaru(グラスウール使用)とガラスファイバー入りパージ剤でパージしました。下記の写真の上段はecomaruの場合で、8ショットで洗浄が終了し、排出された樹脂量は360gでした。(写真は左上から右へ順番に排出された樹脂を並べた様子です。1塊は1ショット分) これに対し、下段はガラスファイバー入りパージ剤でパージした場合で、10ショットで洗浄が終了しました。ここまでの排出量は400gでした。これはecomaruの洗浄性の高さを示しています。こちらは、ecomaruの置換性の高さを示しています。
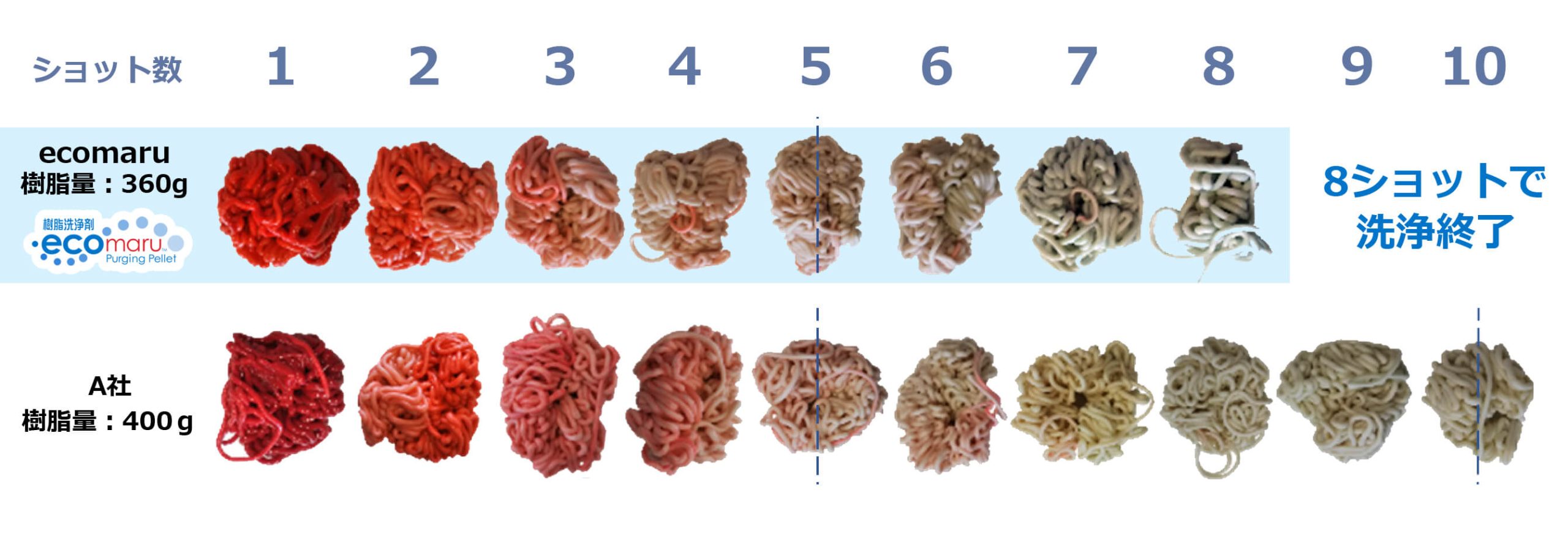
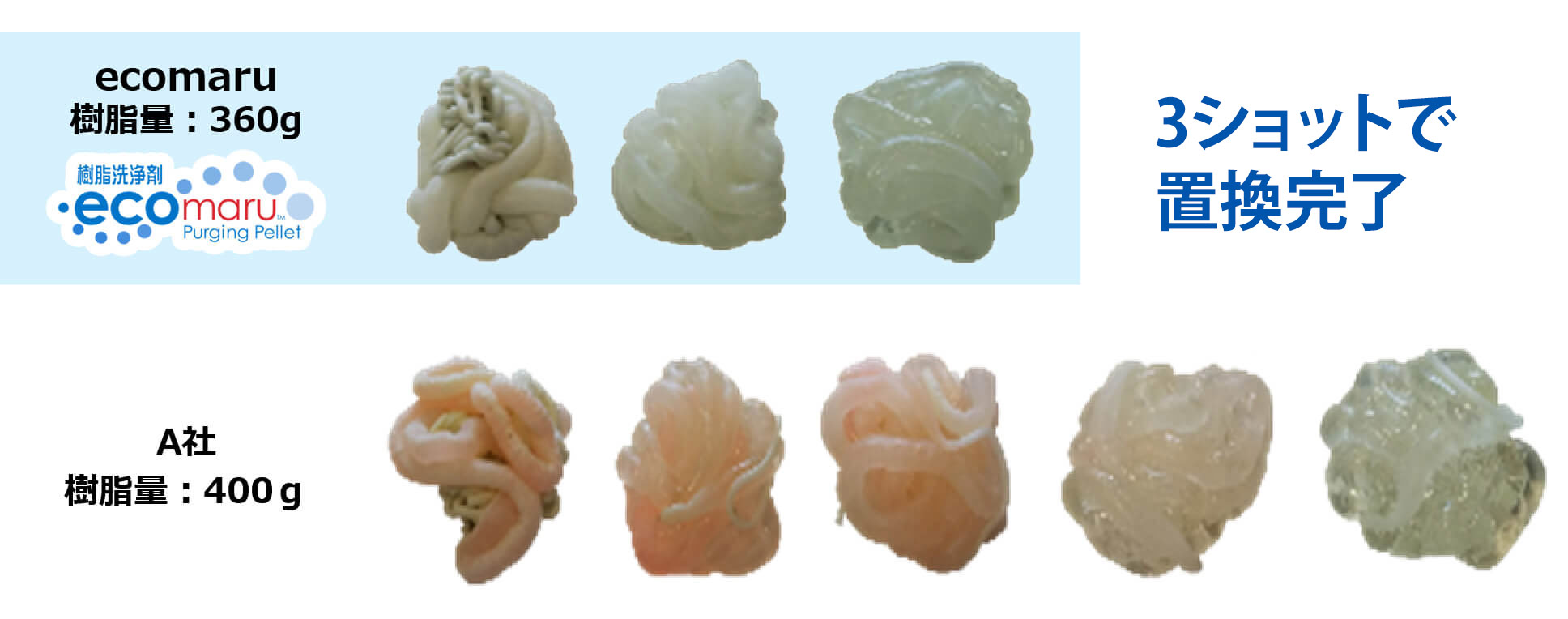
洗浄後、後続樹脂として「AS透明」を使用した場合、パージ剤からの切り替わりを検証しました。ecomaruは3ショットで置換が完了し、A社パージ剤は5ショット必要でした。(さらに、洗浄完了したはずのA社の樹脂には、再度赤色が現れていることが分かります)

二度洗い不要。
リードタイム短縮、コスト削減に貢献。
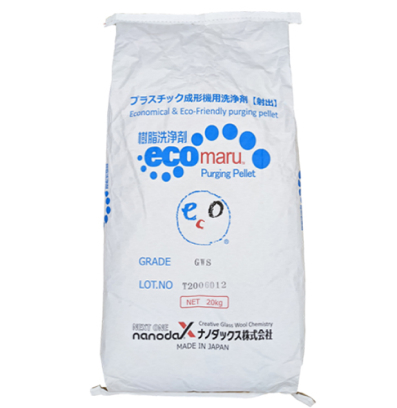
ecomaruは「ガラスフィラー入り洗浄剤」ですが、二度洗いは不要です。※ただし、樹脂によっては二度洗いを行った方が良い場合もあります。
二度洗いとは、ガラスフィラー入りパージ剤で洗浄を行ったあと、後続樹脂にガラスが残らないよう、ガラスフィラー入りではないパージ剤や安価なペレットを使用して再度洗浄を行うことです。ecomaruは1本のガラス繊維が細く短いため、狭いトンネル(ノズル部分など)でも排出性が良く(後続置換性が良い)、通常、二度洗いの必要はありません。
<PP難燃剤入り成形での評価>
下記の成形現場では、GF入パージ剤8kgで洗浄後、PPベースの洗浄剤(5kg)で二度洗いを行っていました。ecomaru(GWPグレード)を用いることで、使用量は8kg⇒7kgと減少し、二度洗いは不要になりました。
前樹脂:PP難燃剤
使用成形機:1300トン射出成形機
置換樹脂:PPナチュラル
前樹脂 | 洗浄剤 | 2度洗い 洗浄剤 | 置換樹脂 | |||
製品名 | 使用量 | 製品名 | 使用量 | |||
従来 | PP難燃 | 他社GF入り | 8kg | 他社PPベース 洗浄剤 |
5kg | PPナチュラル |
ecomaru | PP難燃 | ecomaru 「GWP」 |
7kg | なし | PPナチュラル |
二度洗いがなくなり、また、パージ剤の使用量が減少したことで、46%ほどコスト削減できた結果となりました。
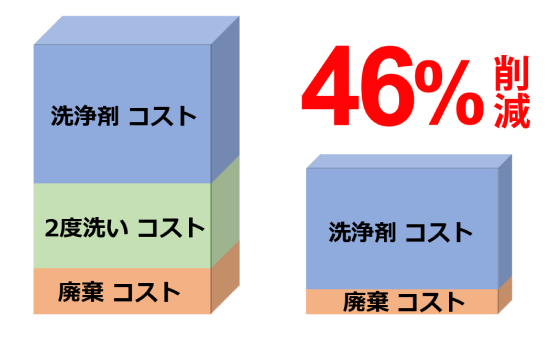
- ガラス排出の2度洗いが無くなった点が大きなコストメリットです。当社はPP成形(色替え)が多い為、PPベースのガラス入り洗浄剤は後材置換に相性が良いと思っています。
- 不良率の減少が図れました。
- 生産性が向上が出来ました。

3グレードで幅広い樹脂に対応。
現場でシンプルな条件で使用できます。
対応樹脂 | PP・PE・GPPS・透明材 | ABS・AS・HIPS・PA6/66・POM・PBT | PC・PC-AMS・PA6T/9T | |
グレード | GSS/GWP | GSS/GWP/GWS | GSS/GWS | |
応用範囲 | 色変え・樹脂種替え | ◎ |
◎ |
〇 |
異物除去 | 〇 | ◎ |
◎ |
|
シール | × | × | × | |
ホットランナー | × | × | × |
グレード | 特徴 | 原料 | 温度範囲 | 適応樹脂 |
GSS | ハイグレード品 炭化物除去 / 色替え / 樹脂替え 最高洗浄力で後続置換性も兼ね備えた オールマイティグレード |
AS+GW | 200 ~ 330℃ | PP・PE・GPPS・PC・PC-ABS ・ PA6T/9T・ABS・AS・HIPS・PA6/66 ・ POM・PBT・透明材 |
GWS | 炭化物除去性重視 適用樹脂・温度帯が広域なバランス重視 |
AS+GW | 200 ~ 320℃ | PC・PC-ABS・PA6T/9T・ABS・AS ・HIPS・PA6/66・POM・PBT |
GWP | オレフィン系ハイグレード品 炭化物除去 / 色替え / 樹脂替え 高洗浄で後続樹脂置換性に優れている |
PP+GW | 180 ~ 280℃ | ABS・AS・HIPS・PA6/66・POM ・PBT・PP・PE・GPPS・透明材 |
GWP…ガラス排出性重視、色替え/樹脂替えに。高洗浄で後続樹脂置換性に優れている(原料:PP+GW)
GWS…炭化物除去性重視。適用樹脂・温度帯が広域なバランス重視(原料:AS+GW)
グレード選定目安
成形温度帯により選定グレードと異なる場合があります。詳しくはお尋ねください。
事例 | 不良率削減 |
検証条件 | ◇ グレード:GWS ◇ 使用樹脂: PP(主)、ナイロン |
課題 | PPからナイロンに樹脂替えする際の黒点が一番の問題 |
評価 | 現パージ剤と比較し、洗浄性の向上、不良率の削減向上が実現できた |
事例 | 黒点不良率激減 |
検証条件 | ◇ グレード:GWS ◇ 成形機容量:100トン ◇ 温度:270℃ ◇ 評価内容:樹脂替え・色替え ◇ 樹脂種類 :ABS(黒) → PC-ABS(ナチュラル) |
課題 | これまで黒点が出ると連続して不良となっていた。 |
評価 | 【検査ご担当者】 ecomaruによるパージ後は、黒点不良が劇的に減り、品質改善が図れました。 【成形ご担当者】 ecomaruの洗浄力に驚きました。同席した営業担当者から事前に、初回利用時には洗浄剤を“通常より多く使用するが、綺麗になるまで洗浄を行う”ようにと話がありました。これまで取れていなかったものがecomaruにより取れ出す現象で、 綺麗になった後、不良率が下がる。という、説明通りとなりました。 |
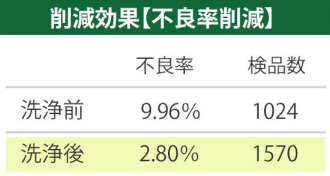
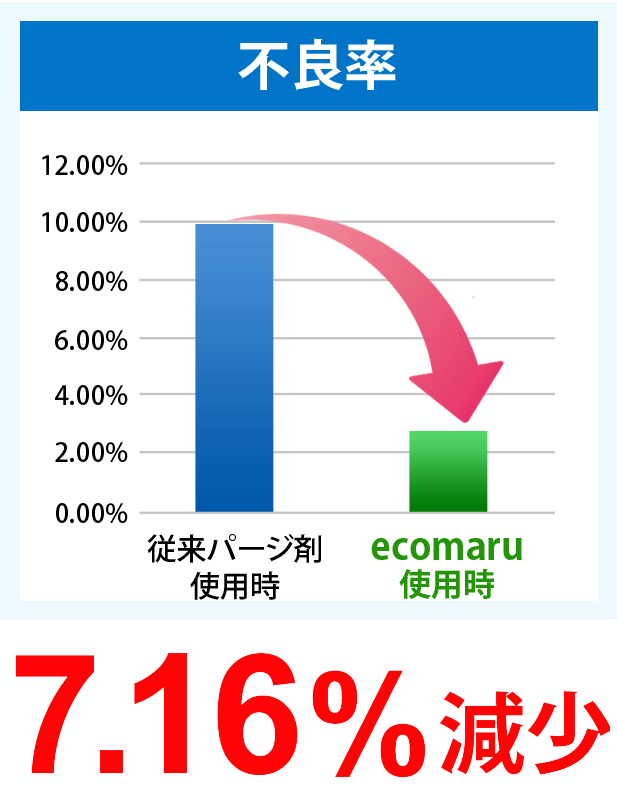