事例2
黒点不良削減
【成形環境】
◇使用グレード:GWS、GWP ◇ 樹脂種類:PP、PS、PE
◇成形機容量 :100トン~550トン
【KEYWORD】作業時間短縮、不良率削減、洗浄時間短縮
使用時の黒点不良率 | 洗浄時間 | パージ剤排出時間 | 分解清掃が必要となる頻度 | |
---|---|---|---|---|
他社GF入りパージ剤 | 5~30% | 30分 | 20分 | 5回/月 |
ecomaru GWS | 0.1~0.2% | 20分 | 15~20分 | 0~1回/月 |
ecomaru GWP | 0.1~0.3% | 20分 | 10~15分 | 1回/月 |
生産管理ご担当者 GWSとGWP両方を採用した理由
両グレードとも共通して「黒点・異物の除去効果」非常に優れていると感じています。
しかし各グレードで一長一短の面もあるため、当社では使い分けて使用することを決定しました。
GWPは不良率をしっかりと抑えつつも、ガラスの残留性が非常に低く、より早く後材料の成形に移れる点を評価しています。
GWSは、不良率の低減率がとにかく高く、分解洗浄回数を減らすのに最適と考え使用しています。
製造ご担当者 評価後のスクリューが衝撃だった。
長年にわたり様々な種類のパージ剤を評価してきましたが、思うような効果を得られた経験がありませんでした。
しかし、ecomaru使用後にスクリューを抜いて残留部を確認したところ、明らかに黒点異物が取れており、衝撃を受けました。
- 界面活性タイプの洗浄剤を使用していたが黒点発生を抑えられず、仕方なく洗浄剤使用後に分解洗浄を行い不良改善に努めていた。
お客様評価
- ecomaruの採用で、黒点不良率が大幅に減少し歩留まりが改善した。それだけでなく、分解洗浄の手間も削減できたため絶大な生産効率の改善が図れた。
- サンプルによる1回テストではなく、ecomaru資料に記載があった通りに複数回テストを実施した。その結果テストを重ねるごとに洗浄効果が表れ不良率削減が実現できた。
客先情報 | |||||||||
---|---|---|---|---|---|---|---|---|---|
顧客名 | 生産品 | 成形機 トン数 | 前樹脂 樹脂 | 色 | 後樹脂 樹脂 | 色 | 導入前課題 | ||||
A社 | 衛生資材 | 非公開 | PP | ナチュラル | GPPS | 白 | 異物不良改善 |
Before | |||||||||
---|---|---|---|---|---|---|---|---|---|
洗浄剤名 | 使用量 | 2度洗い有無 | 黒点不良率 | ||||||
イ社 | 40kg | 無し | 5~30% |
After | |||||||||
---|---|---|---|---|---|---|---|---|---|
洗浄剤名 | 使用量 | 2度洗い有無 | 黒点不良率 | ||||||
ecomaruGWP ecomaruGWS | 30kg | 無し | 0.1% |
事例3
- 界面活性タイプの洗浄剤を使用していたが黒点発生を抑えられず、仕方なく洗浄剤使用後に分解洗浄を行い不良改善に努めていた。
分解清掃 代替
自動車部品成型
【検証条件】
◇ グレード:GWS ◇ 成型機容量:650トン
◇ 温度:230℃ ◇ 評価内容:黒点不良削減
◇樹脂種類:HIPS
【KEYWORD】不良率削減、人的手間削減
お客様課題 : 不良率10%超えると機械を止め分解清掃している。分解にかかる人手と、清掃時間に多く時間を費やしており軽減させたい。
ecomaruによる効果:(1)評価第1弾:炭化物の除去評価
2週間(11日稼働)、毎日1回ecomaruで洗浄実施。使用前と使用後のスクリュ汚れの確認と不良率推移を検証する。
観察条件(ノズルヘッド・スクリュボディ)
エコマル使用前
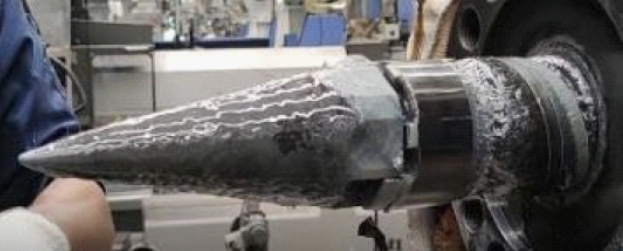
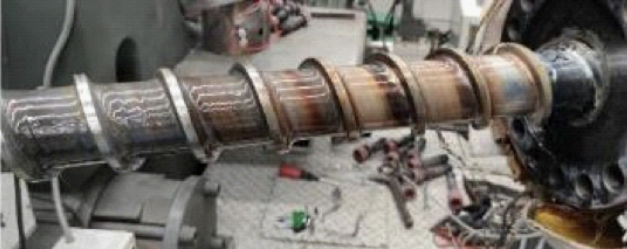
エコマル6日連続使用後
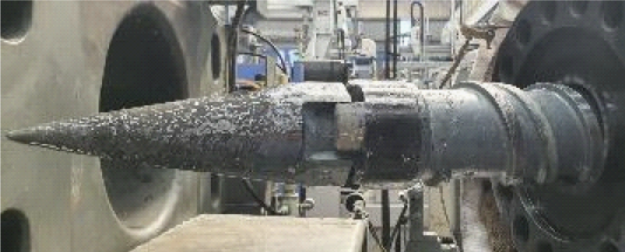
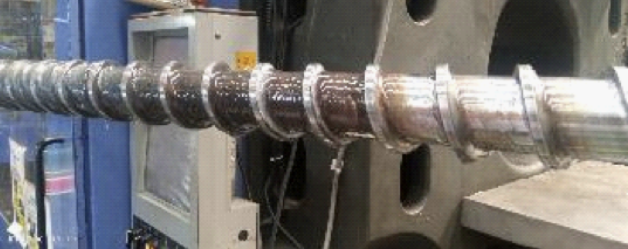
スクリュヘッド・スクリュボディ炭化物がわずかに減少した。
エコマル約2週間(11営業日間)使用後
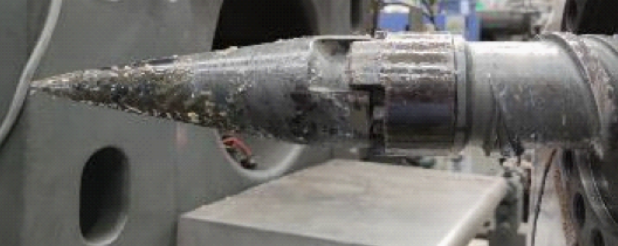
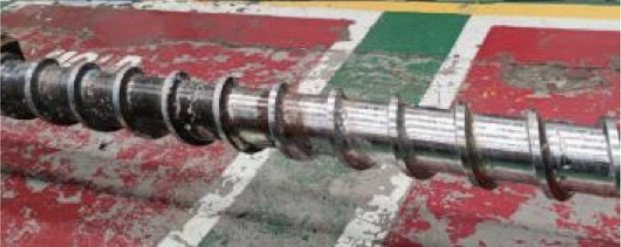
スクリュヘッド・スクリュボディに付着している炭化物が大幅に減少した。
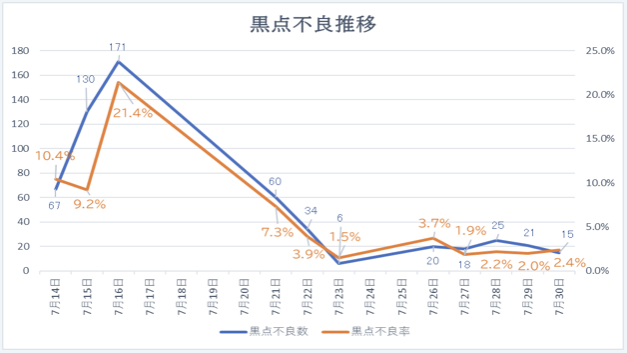
日付 | 黒点 不良数 | 黒点 不良率 | |
---|---|---|---|
7月14日 | 67 | 10.4% | 洗浄開始 |
7月15日 | 130 | 9.2% | - |
7月16日 | 171 | 21.4% | 寝た子を起こす現象発生 |
7月21日 | 60 | 7.3% | 休み明け |
7月22日 | 34 | 3.9% | - |
7月23日 | 6 | 1.5% | - |
7月26日 | 20 | 3.7% | 休み明け |
7月27日 | 18 | 1.9% | - |
7月28日 | 25 | 2.2% | - |
7月29日 | 21 | 2.0% | - |
7月30日 | 15 | 2.4% | - |
【注目点】
①分解清掃の場合
従来、分解清掃後再立ち上げを行った直後は、異物が多く出てきて不良率が極端に上がる。その後落ち着いてくると不良率が抑えられる。
②ecomaruによる洗浄結果
分解清掃時の挙動と同様に、パージ開始直後より不良率が極端に上がった。その後不良率が徐々に下がり、2%台で推移した。
分解清掃時の挙動と同様で、不良率も下がったことで、ecomaruの洗浄効果が分解清掃の代替になることを確認した。
ecomaruによる効果:(2)評価第2弾:不良率の抑止効果
毎日洗浄するのではなく、不良率1%台をキープする為に洗浄頻度(間隔)をどのくらいにするかを検証
評価結果
黒点不良率の記録
「清掃1回 / 2週間」間隔による黒点不良率推移
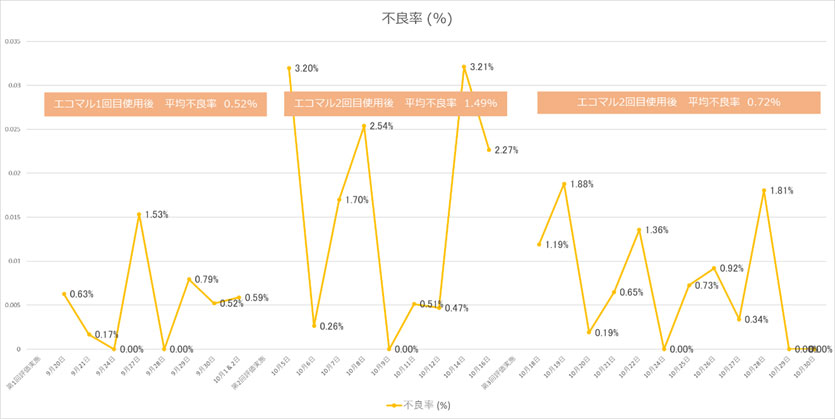
得られた不良率の結果からGWSを使用することで、スクリュをクリーンな状態に保てることが分かった。
評価① ecomaru初回使用から2週間経過時→ 平均黒点不良率/日【0.51%】
評価② ecomaru2回目使用から2週間経過後→ 平均黒点不良率/日【1.49%】
評価③ ecomaru3回目使用から2週間経過後→ 平均黒点不良率/日【0.72%】
不良率1%台をキープする為に洗浄頻度(間隔)をどのくらいにするかを検証した結果、2週間に1度のecomaru洗浄で効果があることが確認できた。
このように、分解洗浄にかかる時間や生産性向上に向けた取り組みを行っている企業様で成果が出ています。また、従来のパージ剤からecomaruを日常的に使用することで、不良率抑制や低減効果を得ている企業様が多数いらっしゃいます。
サンプル評価時には、1度の評価だけではなく、日常的(継続的)に使用してどう推移するかを検証していただくことをお勧めしております。是非お試しください。
事例4
自動車部品成型
洗浄状況
- 従来使用している他社界面活性タイプの洗浄剤でパージを実施。すぐに白色に変わり、パージを終了した。
- その後、 ecomaruに切り替えてパージしたところ、グレー色と黒点が出てきたため、最終的に合計3㎏使用し、終了するまでパージを行った。
お客様評価
検査ご担当者
これまで黒点が出ると連続して不良となっていました。ecomaruによるパージ後は、黒点不良が劇的に減り、品質改善が図れました。
成型ご担当者
ecomaruの洗浄力に驚きました。
同席した営業担当者から事前に、ecomaruの初回利用時には“寝た子を起こす現象”が起こることがあるので注意するようと話がありました。
寝た子を起こすとは「これまで取れていなかったものがecomaruにより取れ出し、使用量目安よりも多く使用する事がある。」という説明でしたがまさにその通りとなりました。
削減効果【不良率削減】
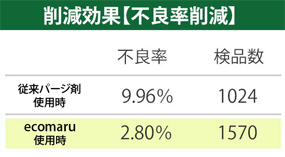
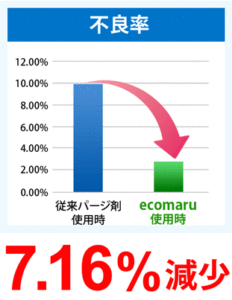
事例5
- 黒点・異物不良が頻繁に発生することに悩んでいる。不良率3%を超えた段階で分解清掃を行っている。
- 様々なパージ剤を試したが大きな効果は得られず非常に困っていた。
お客様評価
- ecomaruを試したところ、成形品への異物混入が激減し、不良率が0.1%で安定するようになった。生産効率の大幅な改善を実現できた。
- 以前使っていた洗浄剤よりも臭いが少なく、作業環境が改善されたため、作業員からも好評。
客先情報 | |||||||||
---|---|---|---|---|---|---|---|---|---|
顧客名 | 生産品 | 成形機 トン数 | 前樹脂 樹脂 | 色 | 後樹脂 樹脂 | 色 | 導入前課題 | ||||
A社 | 工業用 フィルター | 40 | PA66 | 黒 | PA66 | 白 | 異物不良削減 |
Before | |||||||||
---|---|---|---|---|---|---|---|---|---|
洗浄剤名 | 使用量 | 2度洗い有無 | 黒点不良率 | ||||||
A社 | 非公開 | 有 | 0.5~3% |
After | |||||||||
---|---|---|---|---|---|---|---|---|---|
洗浄剤名 | 使用量 | 2度洗い有無 | 黒点不良率 | ||||||
ecomaru GWS | 非公開 | 無 | 0.1% |
燃料(可燃物)
事例6
燃焼グレード
黒点不良率 4% → 1%へ!
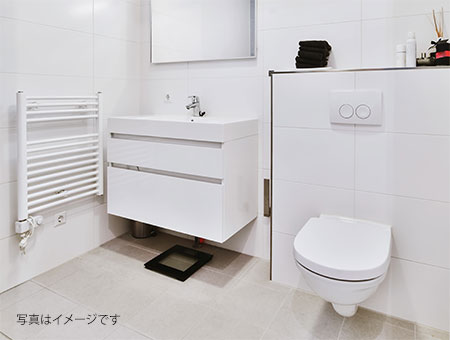
A社:異物不良の改善
製造品の不良基準が厳しく、かつ大物成形であるため、不良が出た際の生産ロスやコストロスが大きいことが課題でした。パージ剤ecomaruへ切替後、異物不良が大幅に減少。生産効率の改善、原料他コストの改善につながりました。
【製品】サニタリー製品部品 【成形機】650t 【前樹脂】PP難燃 【後樹脂】PP難燃
パージ剤 | 黒点不良率 | |
---|---|---|
以前の状況 | 他社製ガラスファイバー入 | 4% |
ecomaru切替後 | ecomaruGWP | 1% |
燃料(可燃物)
事例7
- POMを生産した次の週明けは際に特に異物不良が高く悩んでいた。
- 様々なパージ剤で思考錯誤するも大きな効果が得られなかった
POM(ポリアセタール)
お客様評価
エコマルを使い始めたところ異物不良が5%から0.2%まで減少し、歩留まりを改善できたため、非常に満足している。
Before | |||||||||
---|---|---|---|---|---|---|---|---|---|
洗浄剤名 | 使用量 | 2度洗い有無 | 2度洗い有の場合
洗浄剤名 | 黒点不良率 | |||||
A社 | 3~5% |
After | |||||||||
---|---|---|---|---|---|---|---|---|---|
洗浄剤名 | 使用量 | 2度洗い有無 | 2度洗い有の場合
洗浄剤名 | 黒点不良率 | |||||
ecomaruGWS | 0.20% |
燃料(可燃物)
事例8
- 年間を通してPP成形している機械。これまで生産立ち上げ時に大量の異物が発生して困っていた。
お客様評価
- ecomaruに切替生産を開始したところ、不良率が約1%に抑えられ大幅な歩留まり向上を実現できた。
- 生産立ち上げ時の大掃除用洗浄剤として利用している。
客先情報 | |||||||||
---|---|---|---|---|---|---|---|---|---|
顧客名 | 生産品 | 成形機 トン数 | 前樹脂 樹脂 | 色 | 後樹脂 樹脂 | 色 | 導入前課題 | ||||
B社 | 工業機械 部品 | 100 | PP | 黒 | PE | ナチュラル | 異物不良改善 |
Before | |||||||||
---|---|---|---|---|---|---|---|---|---|
洗浄剤名 | 使用量 | 2度洗い有無 | 黒点不良率 | ||||||
破砕品 | 不明 | 無し | 非開示 |
After | |||||||||
---|---|---|---|---|---|---|---|---|---|
洗浄剤名 | 使用量 | 2度洗い有無 | 黒点不良率 | ||||||
ecomaru GWP | 20kg | 無し | 1.00% |
事例9
- これまで、定期的に異物混入数が増加し著しく生産効率が悪くなる。
お客様評価
- ecomaruを導入したところ異物発生が収まり、生産効率の改善に繋がった。
- 従来パージ剤と比較し、洗浄時間と排出にかかる時間が削減できた。 特に洗浄時間は平均で2割程度の削減できた。
客先情報 | |||||||||
---|---|---|---|---|---|---|---|---|---|
顧客名 | 生産品 | 成形機 トン数 | 前樹脂 樹脂 | 色 | 後樹脂 樹脂 | 色 | 導入前課題 | ||||
A社 | 民生機械 部品 他 | 100 | PC | 黒,白他 | PP,PA ,POM | クリア,白 | 異物不良改善 |
Before | |||||||||
---|---|---|---|---|---|---|---|---|---|
洗浄剤名 | 使用量 | 2度洗い有無 | 黒点不良率 | ||||||
イ社 (GF入り) | 120 | 一部有 | 非開示 |
After | |||||||||
---|---|---|---|---|---|---|---|---|---|
洗浄剤名 | 使用量 | 2度洗い有無 | 黒点不良率 | ||||||
ecomaru GWS | 100 | 一部有 | 非開示 |
事例10
- 異物混入による不良が多発している
- 成形中にたびたび前材の色が混入し、その度に生産を停止せざるを得ない。
お客様評価
- 洗浄剤量使用量と頻度(洗浄回数)は変えていないが、従来不良率が徐々に上がっていっていたのに対し、パージ剤ecomaru切替後は不良率が一定で安定するようになった。
- 前材の色が混入する事がなくなり、生産を停止する事がなくなった。結果として生産性が大幅に向上した。
客先情報 | |||||||||
---|---|---|---|---|---|---|---|---|---|
顧客名 | 生産品 | 成形機 トン数 | 前樹脂 樹脂 | 色 | 後樹脂 樹脂 | 色 | |||||
B社 | 工場設備 パーツ | 220 | PBT | 黒 | PA | 白 |
Before | |||||||||
---|---|---|---|---|---|---|---|---|---|
洗浄剤名 | 使用量 | 2度洗い有無 | 黒点不良率 | ||||||
ロ社 (GF入り) | 非開示 | 有 | 非開示 |
After | |||||||||
---|---|---|---|---|---|---|---|---|---|
洗浄剤名 | 使用量 | 2度洗い有無 | 黒点不良率 | ||||||
ecomaru GWS | 非開示 Beforeと 同量使用 | 有 | 非開示 Before時より 激減 |