World's first! Purging compound using GW (cotton glass fiber)
The glass fibers used in glass filler-infused purging compounds (purging compounds) are commonly referred to as GF (glass fiber). ecomaru uses GW (glass wool), which has finer fibers than GF, to achieve even higher cleaning efficiency. Glass wool has shorter fiber lengths and thinner, softer diameters, allowing the countless glass fiber angles and overwhelming specific surface area to effectively scrape off unwanted materials.
Conventional Purging Compounds
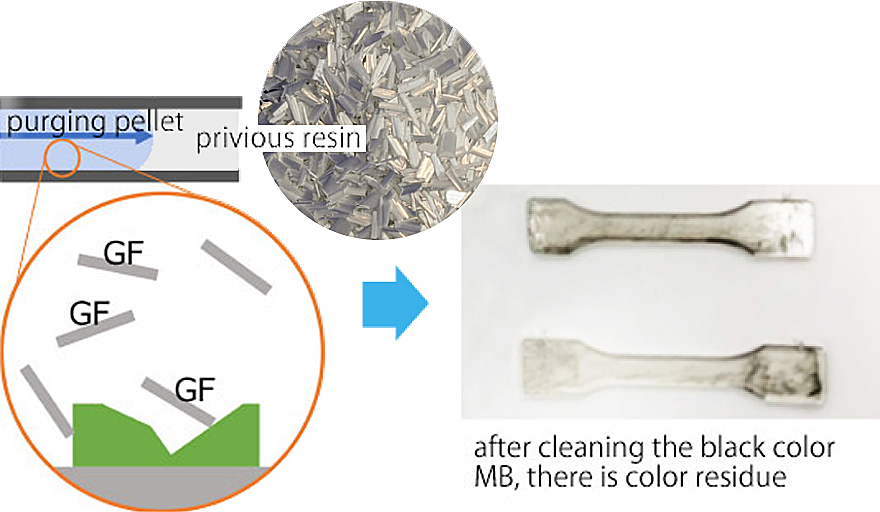
ecomaru
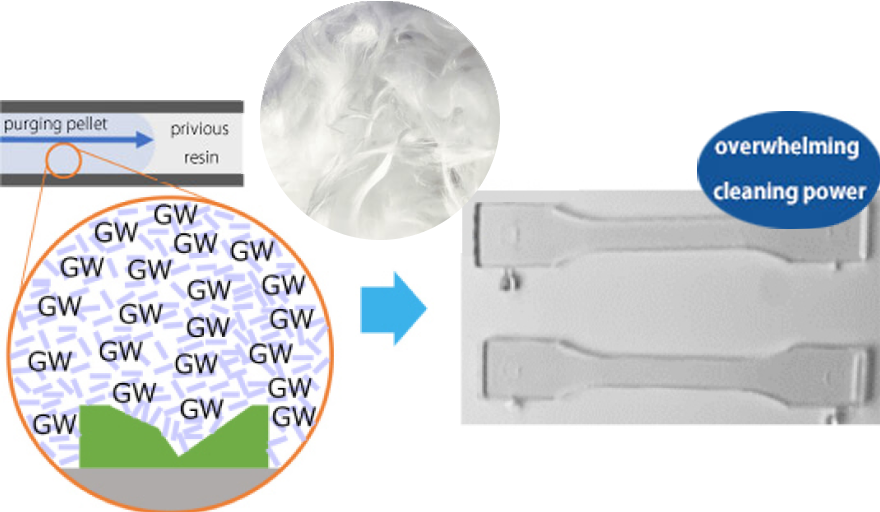
The features of "ecomaru"
The high-cleaning purging compound achieves an unprecedented level of cleanliness. It improves issues with black dots and color residues, contributing to a reduction in defect rates.
Please take a look at the test samples from a major electronics manufacturer. This is a comparison of the cleaning performance with each shot when purging ABS (black). By the fifth shot, you can see that ecomaru shows a darker black. Depending on the cleanliness of the molding machine, the fine glass wool in ecomaru thoroughly cleans the dirt accumulated inside the molding machine, resulting in a darker color compared to other purging compounds when the same number of shots are compared.
Continuing with 10 and 15 shots, ecomaru cleans without any residue left, and by the 15th shot, other purging compounds still show some black residues. A significant difference in cleaning efficiency is observable.
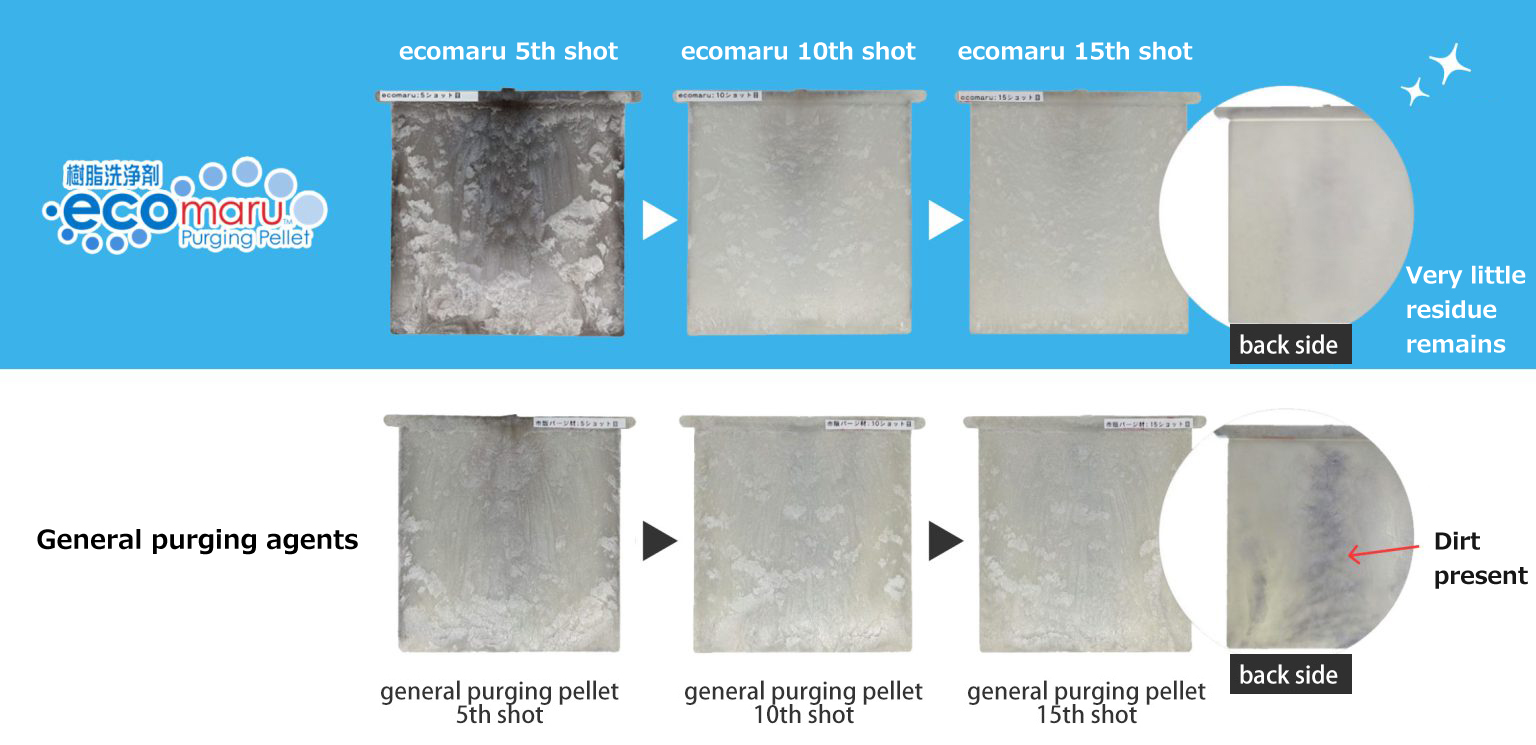
Three grades for a wide range of resins. Can be used under simple conditions on site.
Grade | Features | Raw Materials | Temperature Range | Applicable Resins |
GSS | High-grade product Carbide removal / Color change / Resin change All-purpose grade with the highest cleaning power and replacement capability |
AS+GW | 200 ~ 330℃ | PP・PE・GPPS・PC・PC-ABS・ PA6T/9T・ABS・AS・HIPS・PA6/66・ POM・PBT・Transparent materials |
GWS | Focus on carbide removal Balanced emphasis on a wide range of applicable resins and temperature bands |
AS+GW | 200 ~ 320℃ | PC・PC-ABS・PA6T/9T・ABS・AS・ HIPS・PA6/66・POM・PBT・ PP・PE・GPPS |
GWP | Focus on glass discharge Color change / Resin change High cleaning power and excellent replacement capability for subsequent resins |
PP+GW | 180 ~ 280℃ | PP・PE・GPPS・Transparent materials ABS・AS・HIPS・PA6/66・ POM・PBT |
※Red resin: Material that exhibits particularly high effectiveness
Reduction of black dot defects.
High-cleaning purging compound (purging compound for injection molding machines) ecomaru
In addition to reducing defect rates caused by black dots, other solutions include addressing color residue issues during resin and color changes, and improving glass discharge efficiency to reduce costs.
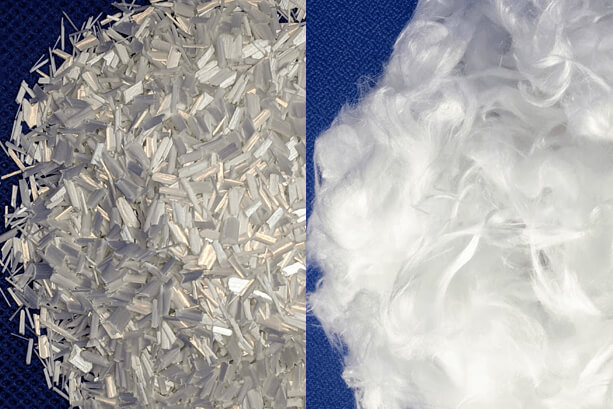
Reduce black dot defects! Features of the high-cleaning purging compound ecomaru
The video explains how the high-cleaning purging compound ecomaru specializes in reducing black dot defects.
What is ecomaru, the purging compound and purging compound for injection molding?
Higher cleaning efficiency than glass fiber-infused purging compounds, reducing black dot defects.
Purging Compounds are resin pellets used to expel (clean) the remaining molding materials, burnt carbides, and dirt from inside the injection molding machine cylinder. They are used for color changes, resin changes, reducing appearance defect rates, and preventing foreign matter generation. There are various types, including surfactant types, foaming types, and glass filler-infused types.
Glass filler-infused purging compounds are more expensive compared to other types, but they are adopted by companies particularly aiming to improve defect rates. They contribute to reducing defect rates in sites molding flame-retardant resins, POM, PC, ABS, and other materials prone to carbide generation, as well as in sites producing large molded products or molded products not requiring painting. Our company has achieved a world-first success in using “glass wool” in purging compounds among glass filler-infused purging compounds. With unprecedented “high cleaning,” we contribute to reducing defect rates in injection molding sites with diverse and small-lot production.
Measures against foreign matter and black dot defects with purging compounds.
Evaluation Method for Purging Compounds
First, please apply for a free evaluation sample (purging compound).
(2) Evaluation Process for Purging Compounds
We introduce the process from requesting an evaluation sample to evaluating the purging compound.
Evaluation Method – Carbide Removal
About the evaluation method for purging compounds aimed at removing black dot defects and carbides.
User feedback on purging compound ecomaru
Case Studies of Black Dot Defect Improvement
Introducing case studies where the high-cleaning purging compound ecomaru achieved improvement in black dot defects.
Case Studies of Cost Reduction
Introducing case studies where the high-cleaning purging compound ecomaru achieved cost reductions, including material replacement vs. purging compound.
Case Studies of Production Efficiency Improvement
Introducing case studies where the high-cleaning purging compound ecomaru improved production efficiency in resin and color changes.
Previously, black dots would lead to continuous defects. After purging with ecomaru, black dot defects dramatically decreased, resulting in significant quality improvement.
Inspection Supervisor
Molding Supervisor
Previously, with GF-infused purging compounds, the remaining glass fibers were a concern, requiring a second purge with a different purging compound. With ecomaru, simply flushing with subsequent resin after purging allows for a smooth transition, significantly reducing costs.
Molding Department Manager
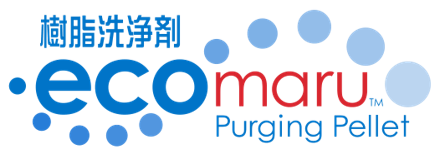
urging pellet (purging compound) “ecomaru” has been using by many plastic molding companies as an alternative for reduction of black dots defect rate, tough stains of dye pigment, disassembling and cleaning.
4-21-19 Higashiogu, Arakawa-ku, Tokyo 116-0012