When considering purging compounds, each customer has various challenges. When evaluating different purging compounds, it is important to first use them according to the manufacturer’s recommended instructions to confirm their effectiveness, and then adapt the usage method to suit your own environment.
Even if the usage method of the purging compound is appropriate, the effect may not be visible unless the “evaluation method” is aligned with the specific challenges. Therefore, we introduce the method to evaluate the “carbide removal effectiveness” of the purging compound ecomaru.
Evaluation Procedure for Carbide Defect Challenges
When expecting a purging compound to have carbide removal effectiveness, it should fundamentally be judged by comparing the frequency of carbide contamination (defect rate). For evaluating this challenge, we recommend the following procedure:
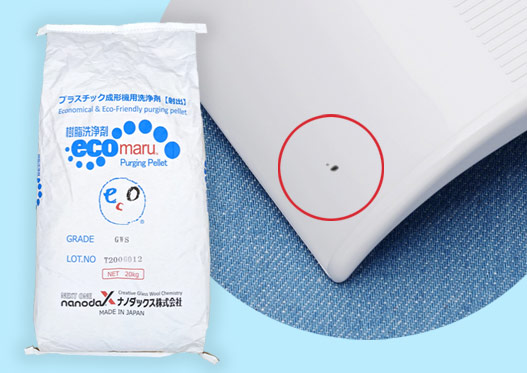
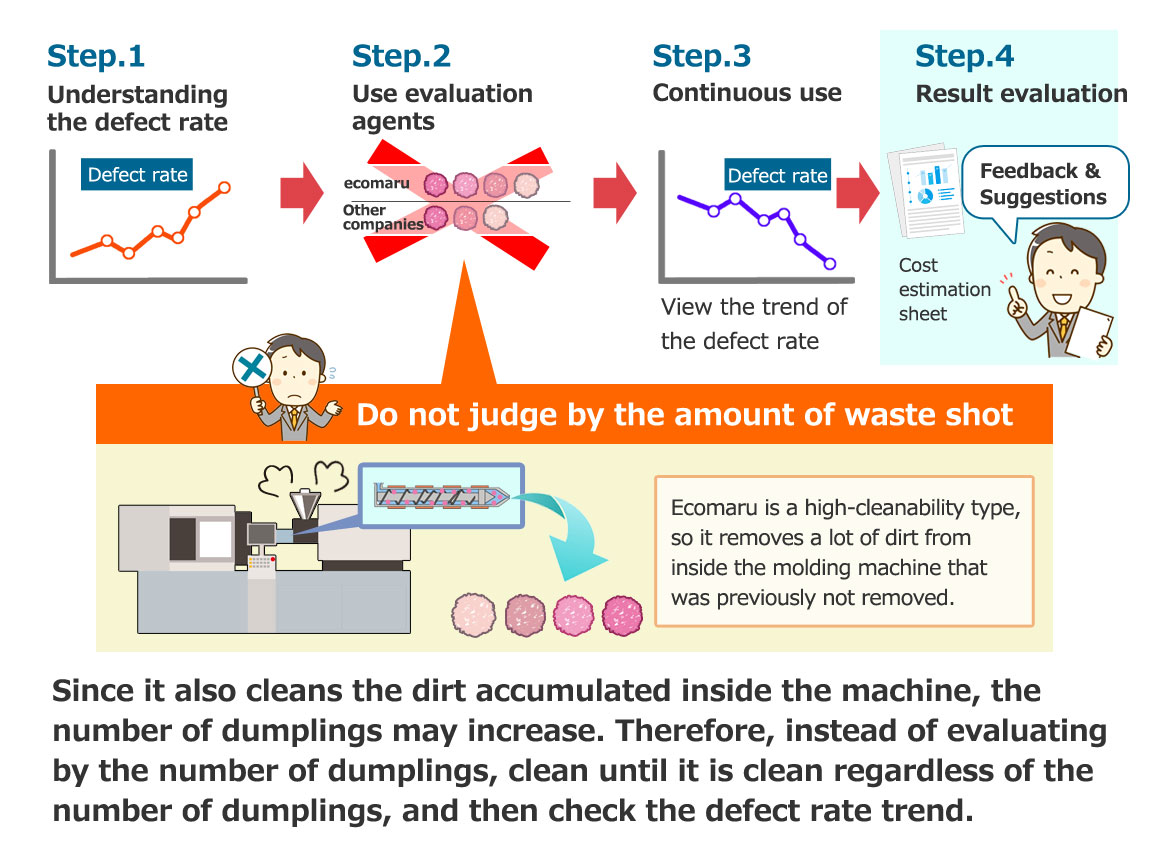
First, before the evaluation, check the usual occurrence of black dots during mass production. If you are not constantly measuring the defect rate, approximate it beforehand. This allows for a more realistic comparison of quantitative defect data. At this time, also check the usual cleaning time and purging compound usage to enable a more comprehensive evaluation.
Case-Specific Points and Additional Notes
During the initial use, defects may frequently occur, and the amount of purging material may be high. If you are considering ecomaru, please inform your representative that you typically do not use purging compounds.
By using a purging compound before dismantling and cleaning, you can visually check the amount of carbides adhering to the machine and make a visual comparison with and without the use of the purging compound. It is recommended to use the purging compound regularly for a few days before dismantling and cleaning. Once the removal effect of carbides is confirmed visually, you can optimize the usage amount by regularly using the purging compound and observing the trend of the defect rate.
Summary
For the evaluation of foreign matter and black dot defect issues, please be mindful of “continuous evaluation” and “quantification of evaluation contents” to conduct a more meaningful review. If you have any questions, please contact us.