
Start of Development of Glass Wool High-Filling Compounding Technology
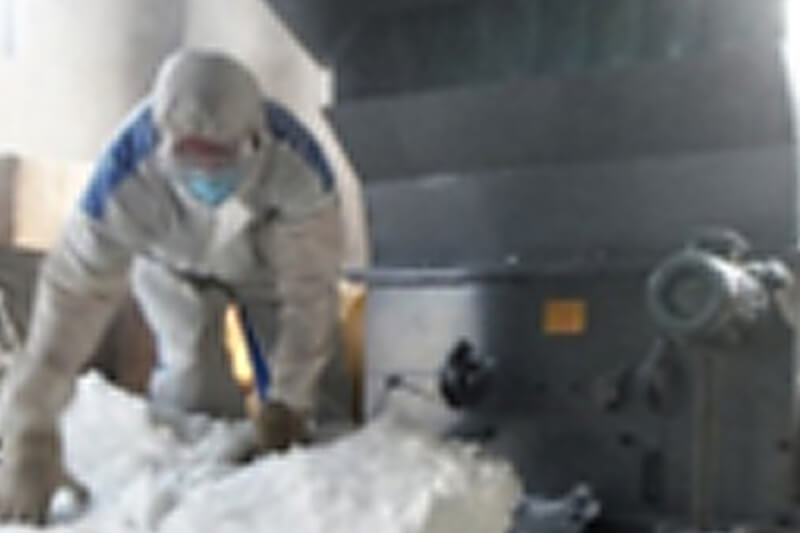
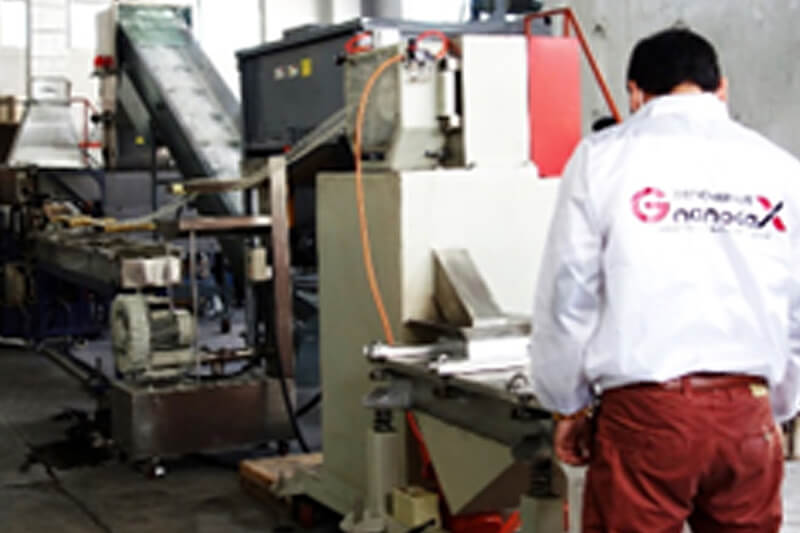
- What Can Be Made with Glass Wool-Filled Material -
- Improvement in strength and rigidity
- Enhanced productivity
- Reduction in shrinkage and warpage
- Superior surface smoothness compared to glass fiber
- Changes in the void phase during foam molding
- Improved sliding properties
- Reduction of burrs
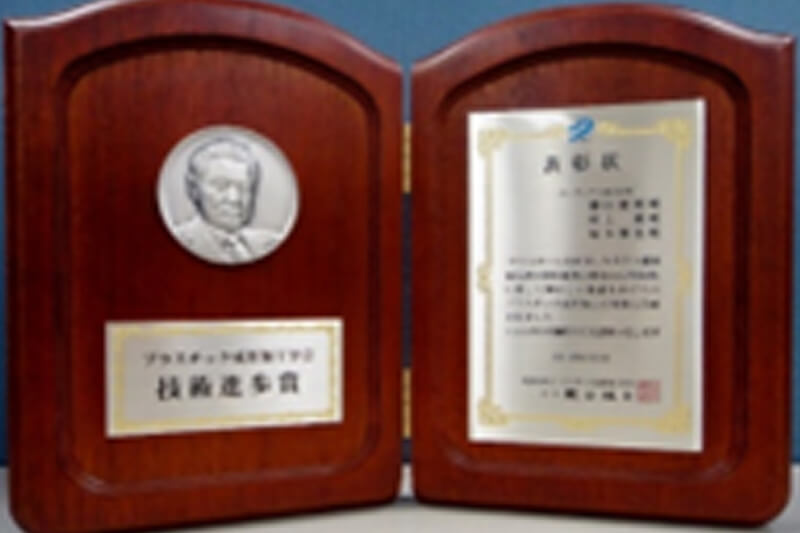

Development of Purging Compound for Plastic Molding Machines 【ecomaru】
To have our materials used, it is necessary to raise awareness of glass wool-filled resins. We were contemplating a product that users could readily use as an initial step. This idea began from a simple remark from a customer:
“We’ve tried various purging compounds, but we are still facing difficulties on-site.”
“Glass fiber-filled purging compounds clean well but damage the molding machine or have poor glass removal.”
We wanted to create a new standard for purging compounds with a new material that does not currently exist. This motivation led to the development. Glass wool is an ultra-fine fiber. We started the development with the idea of leveraging its strengths.
- Like sandblasting, fine fibers can thoroughly clean even the smallest corners.
- The fine and soft fibers can help prevent damage.
- Fine fibers should also contribute to better removal.
Additionally, our company, as an NPO, is engaged in tackling environmental issues. From this background, two key points were considered:
1. Using glass wool offcuts discarded during the manufacturing process can contribute to environmental conservation by reducing waste, while effectively using new glass wool.
2. By using recycled materials in the purging compound itself, customers can also contribute to environmental conservation in their usage environments.
In reality, the performance of the purging compound itself takes precedence over environmental contributions, so it was necessary for our in-house evaluations to exceed the performance of benchmark products.
Through trial and error, we developed Prototype GWS. The actual evaluations from customers were divided into high praise and criticism. Therefore, we made further improvements and launched the current GWS grade. Initially, we anticipated that GWS could be used under various customer environments with just one grade, but it was not that simple. The main challenge was the time required for replacement when switching to olefin-based resins. To address this issue, we introduced the GWP grade.
On March 23, 2023, in Arakawa Ward, where our company is based, an awards ceremony for the New Product and New Technology Grand Prize was held. Our purging compound for plastic molding machines, ecomaru, received the highest award. Today, in addition to domestic customers, it has gained a reputation in Asia and Europe and is being adopted widely.
Currently, at the new factory, we are working on improving the color of the GWS/GWP grades and preparing for a third new grade.
The president himself is advancing the work, covered in glass fibers on site. Visitors who come to see the site are always surprised and greet him with astonishment.
I asked the president why he was so involved in the field.
“Because until it is recognized as a new standard, I have to achieve it myself.”
“Even if people laugh and ask what I’m doing on-site, I’ll see it through! Focusing on customers and the field has been our tradition since the chairman’s era.”
Although we are a small company, with the slogan “Someday to the world,” we are committed to glass wool-filled materials and continue to strive daily.
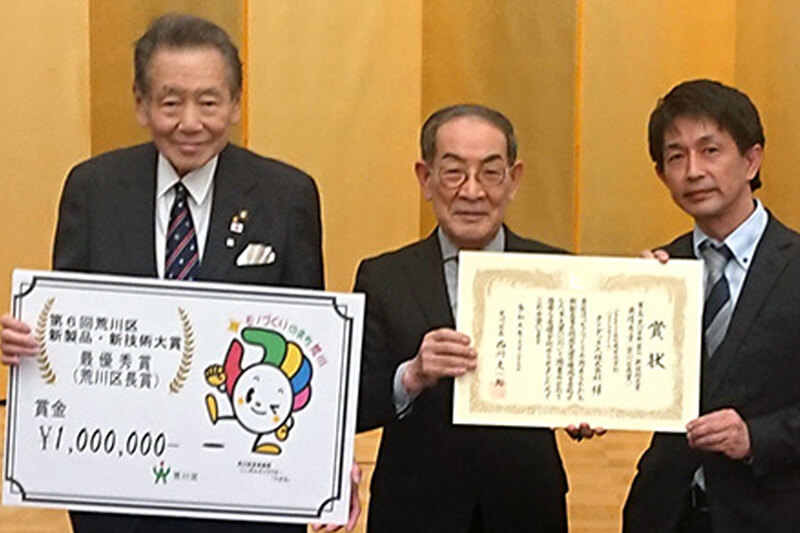