Case 1
Reduction of color change, resin change, and startup time
【KEYWORD】Reduction of defect rate
【Molding Environment】
◇ Usage Grade: GWS, GWP
◇ Molding Machine Capacity: Small to Large
◇ Resin Types: PA66, PBT, PC, etc.
Reduction Effect 【Defect Rate Reduction】
Black Dot Defect Rate | |
---|---|
Before Use | 30% |
After Use | 10% |
Molding Personnel
We didn’t have any major concerns, but we often produce small quantities of various products, leading to significant purge agent usage, appearance defect rates, and downtime during changeovers. When a large number of black dots appeared during machine shutdown, we evaluated ecomaru in hopes of reducing defects. We observed effects not seen with existing products, resulting in a very quick production start.
Molding Personnel from Another Plant
Due to the quick removal of previous materials, we significantly reduced the usage of purge agents. Additionally, ecomaru has minimal glass wool residue even during changeovers with large temperature differences, eliminating the need to use multiple purge agents, making it convenient. It was also effective for cleaning GF-filled materials, which used to take a lot of time to clean.
Case 2
- Purge agents are used during production startup. For black molded products, foreign matter affects the shape of the molded products, making countermeasures against foreign matter essential.
- Previously, we used multiple types of purge agents and performed double cleaning without GF at the end, which took about 3 hours to start up.
Customer Evaluation
- ecomaru combines cleaning performance and discharge efficiency, allowing us to maintain the same defect rate with a single cleaning.
- As a result, the usage of purge agents was reduced by approximately half. Additionally, the time required for a single cleaning was reduced to about one-third, achieving significant cost reduction and increased production volume.
Customer Information | |||||||||
---|---|---|---|---|---|---|---|---|---|
Customer Name | Production Items | Molding Machine Tonnage | Previous Resin Resin | Color | Subsequent Resin Resin | Color | Challenges Before Implementation | ||||
Company B | Automotive Parts | Large Machine (Confidential) | PC Alloy | Black | PC Alloy | Black | Reduction of Cleaning Costs |
Before | |||||||||
---|---|---|---|---|---|---|---|---|---|
Purging Compound Name | Usage Amount | Double Cleaning Presence | Black Dot Defect Rate | ||||||
① Company R (with GF) ② Multiple Other Purge Agents | Non-disclosure | Present | 1.00% |
After | |||||||||
---|---|---|---|---|---|---|---|---|---|
Purging Compound Name | Usage Amount | Double Cleaning Presence | Black Dot Defect Rate | ||||||
ecomaru GWS | Non-disclosure | Absent | 1.00% |
Case 3
Home Appliance Molding
Customer Evaluation
- Previously, we were concerned about glass fiber residue with conventional GF-containing purging compounds, requiring two purges with different purging compounds. With ecomaru, switching can be achieved simply by discarding the post-purge resin, significantly reducing costs.
- For large machines, there was considerable smoke production, and we had to work while being mindful of fire alarms. ecomaru produces much less smoke, which is very beneficial. Additionally, the odor has been greatly reduced.
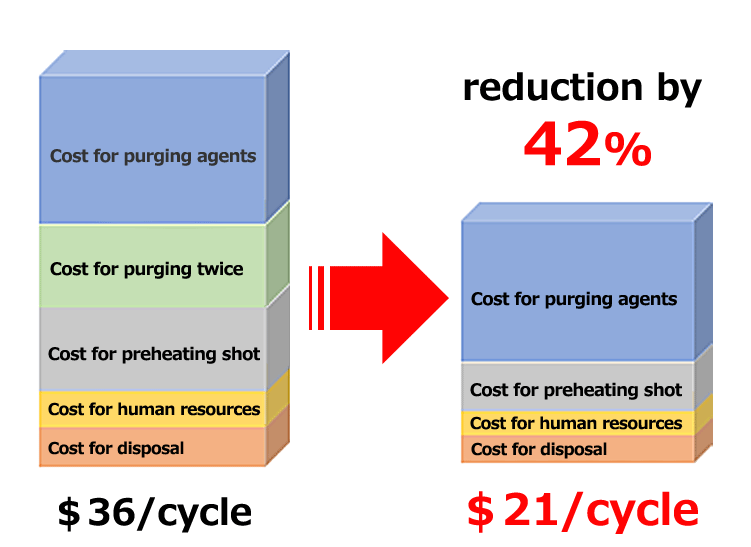
Reduction Effect 【Total Cost】
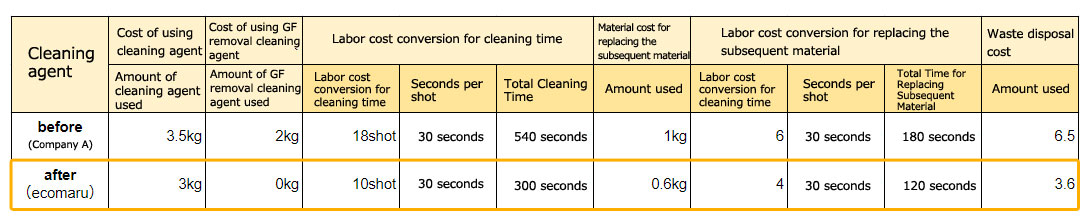
Case 4
- Due to production requirements, we had to mold resins with significantly different colors and molding temperatures using the same machine, resulting in frequent contamination and color mixing in the molded products. Although countermeasures are taken each time, the defect rate gradually increases, making it difficult to stabilize the yield.
Customer Evaluation
- By using ecomaru, various defects improved from the first day, reducing by about half and significantly improving production efficiency.
- The cleaning time was reduced to about 30% compared to other products. It is easy to use, and we have completely switched to it.
Customer Information | |||||||||
---|---|---|---|---|---|---|---|---|---|
Customer Name | Production Items | Molding Machine Tonnage | Previous Resin Resin | Color | Subsequent Resin Resin | Color | Challenges Before Implementation | ||||
Company B | Industrial Equipment Parts | 350 | ABS | Black | PP | Black | Contamination Defect Improvement |
Before | |||||||||
---|---|---|---|---|---|---|---|---|---|
Purging Compound Name | Usage Amount | Double Cleaning Presence | Black Dot Defect Rate | ||||||
Ha Company (GF-filled) | 30 kg | None | 6.00% |
After | |||||||||
---|---|---|---|---|---|---|---|---|---|
Purging Compound Name | Usage Amount | Double Cleaning Presence | Black Dot Defect Rate | ||||||
ecomaru GWS | 20 kg | None | 3.00% |
Case 5
PP Flame Retardant Molding
Customer Evaluation
- The elimination of double washing for glass discharge is a significant cost benefit. Since we frequently mold PP (color changes), we find that PP-based glass-filled purging compounds are well-suited for subsequent material replacement.
- We have achieved a reduction in the defect rate.
- Productivity has improved.
Reduction Effect 【Cleaning Cost Reduction】
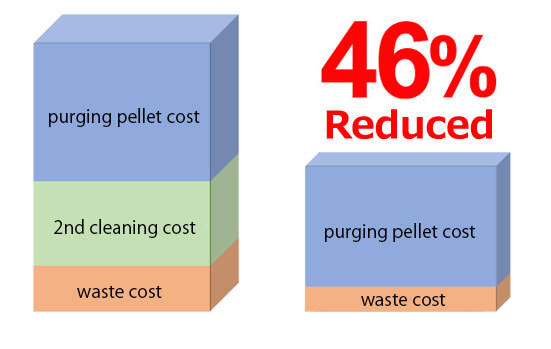
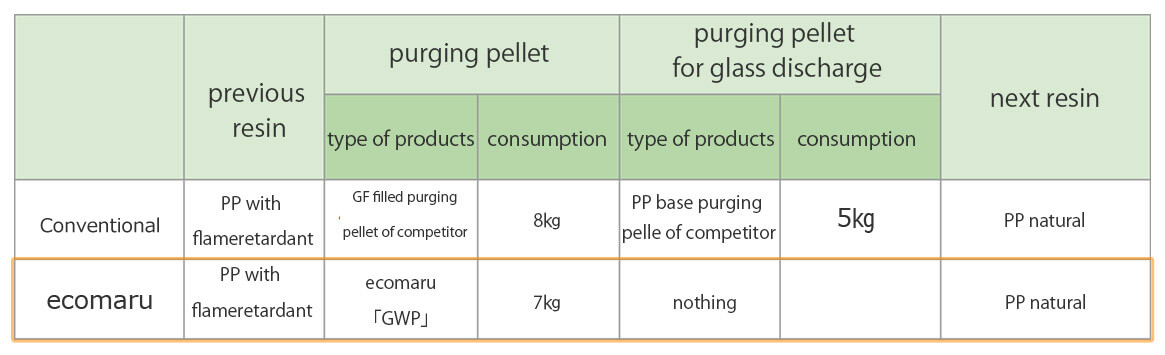
Case 6
- The previous purging compounds had good cleaning power but were difficult to discharge, resulting in longer material changeover times.
Customer Evaluation
- After trying ecomaru, the usage of purging compounds was reduced by approximately 30%. Additionally, the time required for material replacement, which was a challenge, was reduced by about 40%, leading to significant improvement.
- We were able to quickly transition to production, successfully reducing the costs of purging compounds and discarded shots.
Customer Information | |||||||||
---|---|---|---|---|---|---|---|---|---|
Customer Name | Production Items | Molding Machine Tonnage | Previous Resin Resin | Color | Subsequent Resin Resin | Color | Challenges Before Implementation | ||||
Company C | Automotive Parts | 650~ | PP | Black | PP | White | Purging Compound Usage & Setup Time Reduction |
Before | |||||||||
---|---|---|---|---|---|---|---|---|---|
Purging Compound Name | Usage Amount | Double Cleaning Presence | Black Dot Defect Rate | ||||||
Ro Company (GF-filled) | 300 kg | None | Non-disclosure |
After | |||||||||
---|---|---|---|---|---|---|---|---|---|
Purging Compound Name | Usage Amount | Double Cleaning Presence | Black Dot Defect Rate | ||||||
ecomaru GWP | 200kg | None | Non-disclosure |
Case 7
- Currently, we use GF-filled purging compounds, followed by a second wash with GF-free purging compounds. We aim to reduce the usage of purging compounds and setup time.
Customer Evaluation
- After trying ecomaru, we found that the discharge of the previous material was completed with about half the usage compared to other GF-filled purging compounds. Additionally, with ecomaru, the double washing with a separate purging compound was no longer necessary, reducing the usage of purging compounds by about half.
- With other GF-filled purging compounds, it was necessary to heat up the molding machine before starting the cleaning process, which took a significant amount of time before beginning the molding of low-temperature resins. ecomaru did not require heating, significantly reducing the changeover time.
Customer Information | |||||||||
---|---|---|---|---|---|---|---|---|---|
Customer Name | Production Items | Molding Machine Tonnage | Previous Resin Resin | Color | Subsequent Resin Resin | Color | Challenges Before Implementation | ||||
Company A | Home Appliance Parts | 100 | ABS | Black | PS | Natural | Purging Compound Usage & Setup Time Reduction |
Before | |||||||||
---|---|---|---|---|---|---|---|---|---|
Purging Compound Name | Usage Amount | Double Cleaning Presence | Black Dot Defect Rate | ||||||
I Company (GF-filled) | 40 kg | Ro Company 40 kg | Non-disclosure |
After | |||||||||
---|---|---|---|---|---|---|---|---|---|
Purging Compound Name | Usage Amount | Double Cleaning Presence | Black Dot Defect Rate | ||||||
ecomaru GWS | 20 kg | None | Non-disclosure |
Case 8
Flame Retardant Grade
Improvement in Production Efficiency
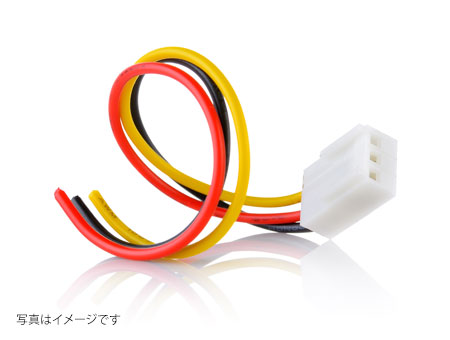
Reduction in Resin and Color Changeover Time
We often produced flame-retardant resins and had a high rate of black dot defects, but the bigger issue was poor replaceability. After switching to ecomaru, the cleaning time was reduced to about half. This led to reduced production time, usage, and waste. 【Product】Industrial parts for distribution boards, etc. 【Molding Machine】100t 【Previous Resin】PBT Flame Retardant (Black) 【Subsequent Resin】PBT Flame Retardant (Transparent)
Purging Compound | Purging Compound Usage | |
---|---|---|
Previous Situation | No Glass Fiber from Other Manufacturers | 150~200 kg/month |
After Switching to ecomaru | ecomaruGWS | 100 kg/month |
燃料(可燃物)
Case 9
- We want to reduce the cost of purging compounds.
Customer Evaluation
- The unit price can be reduced compared to conventional purging compounds.
- The previous material residue, which could not be removed by conventional purging compounds, was eliminated, resulting in a 50% reduction in contamination defects.
- The work time required for a single resin change was reduced by about 3 minutes per occurrence, achieving total cost reduction through the combination of 【unit cost × reduction in cleaning time and usage × reduction in defect rate】.
Customer Information | |||||||||
---|---|---|---|---|---|---|---|---|---|
Customer Name | Production Items | Molding Machine Tonnage | Previous Resin Resin | Color | Subsequent Resin Resin | Color | Challenges Before Implementation | ||||
Company B | Automotive Parts | 1050 | PA6 | Black | PA66 | Black | Cost Improvement |
Before | |||||||||
---|---|---|---|---|---|---|---|---|---|
Purging Compound Name | Usage Amount | Double Cleaning Presence | Black Dot Defect Rate | ||||||
Company B | Not Disclosed | PP | 0.35% |
After | |||||||||
---|---|---|---|---|---|---|---|---|---|
Purging Compound Name | Usage Amount | Double Cleaning Presence | Black Dot Defect Rate | ||||||
ecomaru GWS | 10% Reduction Compared to Before | PP | 0.03% |