Case Study 1
Molding of Air Conditioning-Related Components
- The total quantity was reduced by 10-20% compared to the conventional GF-containing purge agent.
- The results were particularly significant with larger molding machines, where the usage of glass-containing purge agent was reduced by up to 50%.
- The rinsing of glass [GF] (double washing) was discontinued.
Black Dot Defects
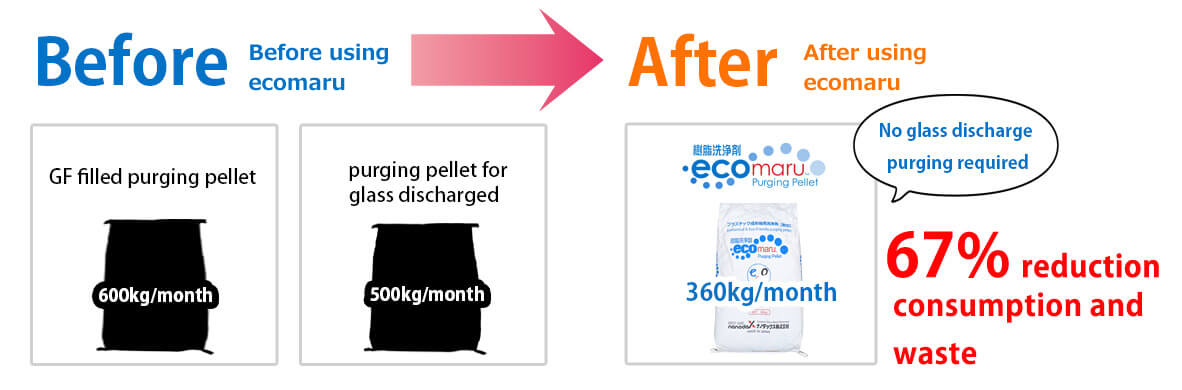
Reduction Effect
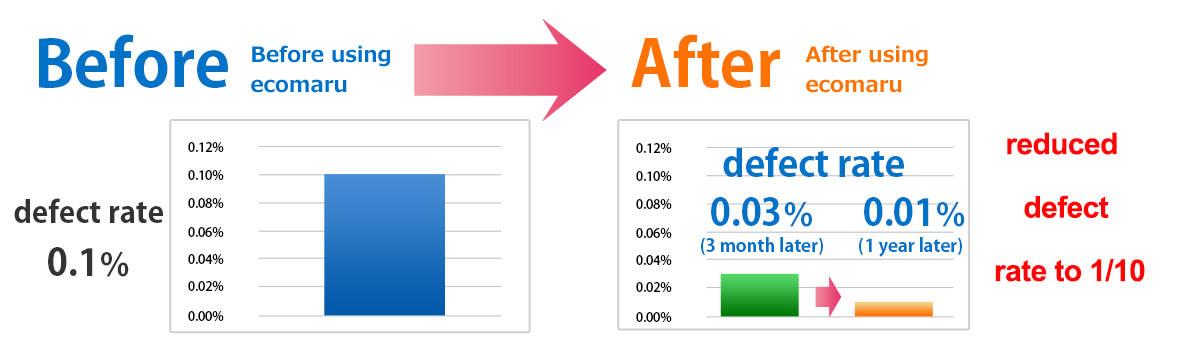
Case Study 2
Reduction of Black Dot Defects
Defect Rate of Black Dots During Use | Cleaning Time | Purge Agent Discharge Time | Frequency of Required Disassembly Cleaning | |
---|---|---|---|---|
Other Companies' GF-Containing Purge Agents | 5–30% | 30 minutes | 20 minutes | 5 times/month |
ecomaru GWS | 0.1-0.2% | 20 minutes | 15–20 minutes | 0–1 time/month |
ecomaru GWP | 0.1-0.3% | 20 minutes | 10-15 minutes | 1 times/month |
Reasons for Adopting Both GWS and GWP
Both grades have a common feature: “Excellent in removing black dots and foreign substances.” However, each grade has its strengths and weaknesses, so we decided to use them selectively in our company. We value GWP for its ability to significantly reduce defect rates while also having very low glass residue, allowing for quicker transition to molding the next material. On the other hand, GWS is highly effective in reducing defect rates and is ideal for minimizing the frequency of disassembly cleaning.
Manufacturing Supervisor: The impact on the screw after evaluation was astonishing.
Over the years, we have evaluated various types of purge agents but have never experienced the desired effect. However, after using ecomaru and checking the residual part by removing the screw, we were amazed to see that the black dots and foreign substances were clearly removed.
- We had been using surfactant-type purging compounds, but they were unable to prevent the occurrence of black dots. As a result, we had no choice but to perform disassembly cleaning after using the purging compound in an effort to improve defect rates.
Customer Evaluation
- With the adoption of ecomaru, the defect rate due to black dots has significantly decreased, leading to improved yield. Additionally, the reduced need for disassembly cleaning has greatly enhanced production efficiency.
- Rather than conducting just a single test with the sample, we performed multiple tests as indicated in the ecomaru documentation. As a result, the cleaning effect became more evident with each test, leading to a significant reduction in defect rates.
Customer Information | |||||||||
---|---|---|---|---|---|---|---|---|---|
Customer Name | Products Produced | Molding Machine Capacity (tons) | Previous Resin Resin | Color | Subsequent Resin Resin | Color | Issues Before Implementation | ||||
Company A | Sanitary Materials | Not Disclosed | PP | Natural | GPPS | White | Improvement of Foreign Matter Defects |
Before | |||||||||
---|---|---|---|---|---|---|---|---|---|
Purging Compound Name | Usage Amount | Whether Double Washing is Performed | Defect Rate of Black Dots | ||||||
Company I | 40 kg | None | 5-30% |
After | |||||||||
---|---|---|---|---|---|---|---|---|---|
Purging Compound Name | Usage Amount | Whether Double Washing is Performed | Defect Rate of Black Dots | ||||||
ecomaruGWP ecomaruGWS | 30 kg | None | 0.1% |
Case Study 3
- We had been using surfactant-type purging compounds, but they were unable to prevent the occurrence of black dots. As a result, we had no choice but to perform disassembly cleaning after using the purging compound in an effort to improve defect rates.
Disassembly Cleaning Alternative
Automotive Parts Molding
【Verification Conditions】
◇ Grade: GWS ◇ Molding Machine Capacity: 650 tons
◇ Temperature: 230°C ◇ Evaluation Content: Reduction of Black Dot Defects
◇ Resin Type: HIPS
【KEYWORDS】Reduction of Defect Rate, Reduction of Manual Labor
Observation Conditions (Nozzle Head & Screw Body)
Before Using ecomaru
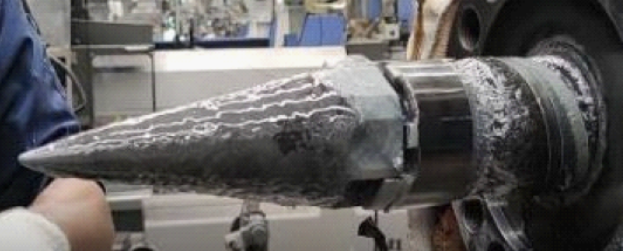
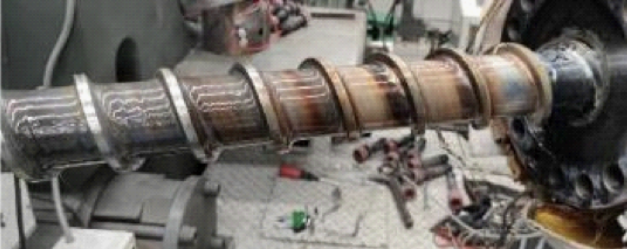
After 6 Consecutive Days of Using ecomaru
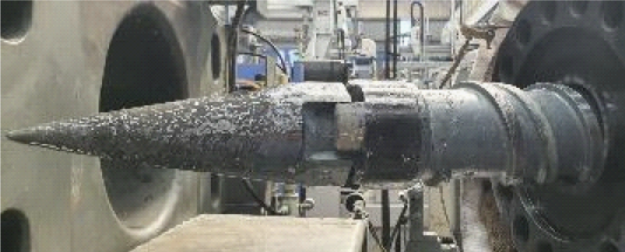
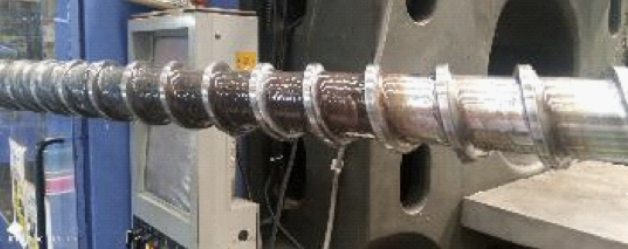
After Approximately Two Weeks (11 Business Days) of Using ecomaru
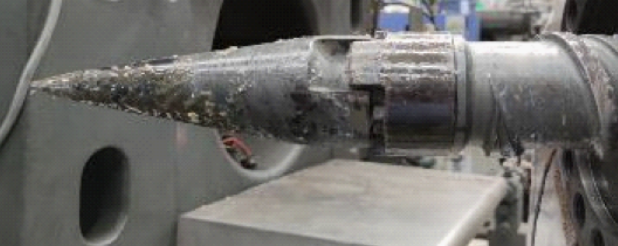
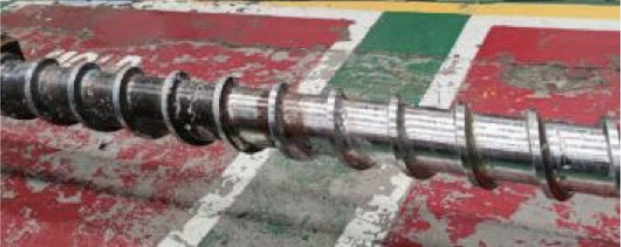
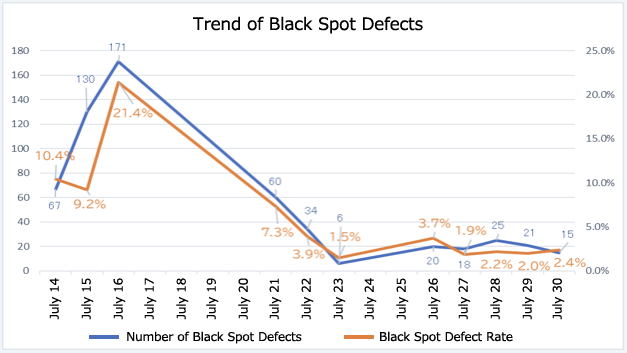
Date | Black Dot Defect Count | Black Dot Defect Rate | |
---|---|---|---|
July 14 | 67 | 10.4% | Start of Cleaning |
July 15 | 130 | 9.2% | - |
July 16 | 171 | 21.4% | Occurrence of "Awakening the Sleeping Child" Phenomenon |
July 21 | 60 | 7.3% | After the Holiday |
July 22 | 34 | 3.9% | - |
July 23 | 6 | 1.5% | - |
July 26 | 20 | 3.7% | After the Holiday |
July 27 | 18 | 1.9% | - |
July 28 | 25 | 2.2% | - |
July 29 | 21 | 2.0% | - |
July 30 | 15 | 2.4% | - |
【Points of Interest】
② Cleaning Results with ecomaru: Similar to the behavior observed during disassembly cleaning, the defect rate spiked sharply right after the start of purging. Subsequently, the defect rate gradually decreased, stabilizing at around 2%. This similar behavior and the subsequent reduction in defect rate confirmed that the cleaning effect of ecomaru can serve as an alternative to disassembly cleaning.
Effects of ecomaru: (2) Second Evaluation: Defect Rate Suppression
Instead of daily cleaning, we investigated the optimal cleaning frequency (interval) required to maintain the defect rate at around 1%.
Evaluation Results
Record of Black Dot Defect Rate
Trend in Black Dot Defect Rate with “Cleaning Once Every Two Weeks” Interval
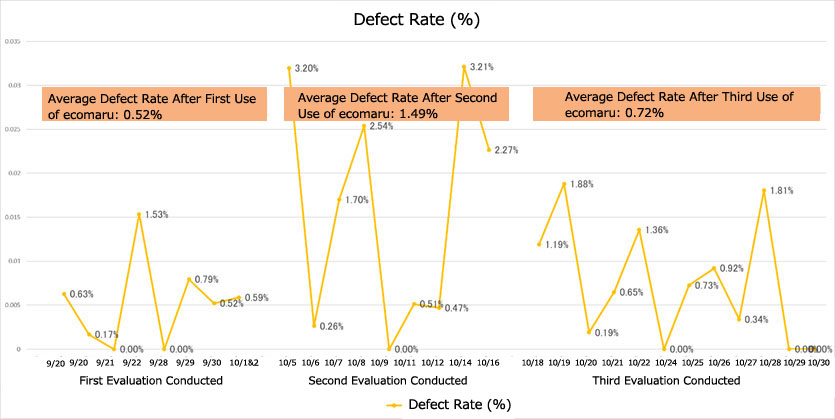
Evaluation ① After 2 weeks from the first use of ecomaru → Average daily black dot defect rate: 【0.51%】
Evaluation ② After 2 weeks from the second use of ecomaru → Average daily black dot defect rate: 【1.49%】
Evaluation ③ After 2 weeks from the third use of ecomaru → Average daily black dot defect rate: 【0.72%】
Case Study 4
Automotive Parts Molding
Cleaning Status
- The purge was carried out using a conventional surfactant-type purging compound from another company. The purge was stopped as soon as the color turned white.
- After switching to ecomaru and purging, gray color and black dots appeared, so a total of 3 kg was used to complete the purge.
Customer Evaluation
Inspector in Charge
Previously, continuous defects occurred when black dots appeared. After the purge with ecomaru, the occurrence of black dot defects drastically decreased, resulting in improved quality.
I was amazed by the cleaning power of ecomaru. The sales representative present informed us beforehand to be cautious, as the “awakening of a dormant issue” might occur during the first use of ecomaru. This phenomenon, as explained, means that residues previously not removed may be dislodged by ecomaru, potentially leading to higher usage than the recommended amount. This was precisely what happened.
Reduction Effect 【Defect Rate Reduction】
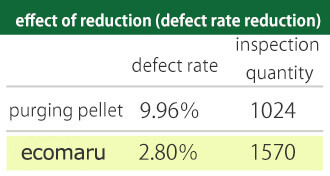
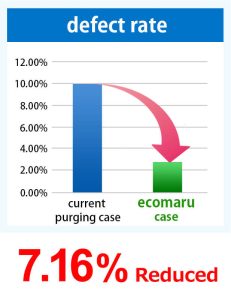
Case Study 5
- Frequent occurrences of black dots and foreign matter defects have been a concern. Decomposition cleaning is performed when the defect rate exceeds 3%.
- We tried various purging compounds, but none had a significant effect, leaving us very troubled.
Customer Evaluation
- After trying ecomaru, the contamination of molded products was drastically reduced, and the defect rate stabilized at 0.1%. This led to a significant improvement in production efficiency.
- It has less odor compared to the previous purging compounds we used, improving the working environment, which has been well-received by the workers.
Customer Information | |||||||||
---|---|---|---|---|---|---|---|---|---|
Customer Name | Products Produced | Molding Machine Capacity (tons) | Previous Resin Resin | Color | Subsequent Resin Resin | Color | Issues Before Implementation | ||||
Company A | Industrial Filter | 40 | PA66 | Black | PA66 | White | Reduction of Foreign Matter Defects |
Before | |||||||||
---|---|---|---|---|---|---|---|---|---|
Purging Compound Name | Usage Amount | Whether Double Washing is Performed | Defect Rate of Black Dots | ||||||
Company A | Not Disclosed | Exists | 0.5-3% |
After | |||||||||
---|---|---|---|---|---|---|---|---|---|
Purging Compound Name | Usage Amount | Whether Double Washing is Performed | Defect Rate of Black Dots | ||||||
ecomaru GWS | Not Disclosed | None | 0.1% |
燃料(可燃物)
Case Study 6
Combustion Grade
Black dot defect rate reduced from 4% to 1%!
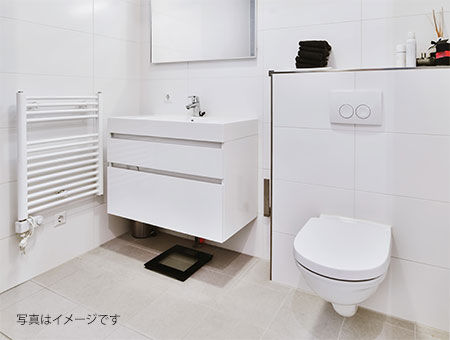
Company A: Improvement in foreign matter defects
The strict defect criteria and large molded products resulted in significant production and cost losses when defects occurred. After switching to the purging compound ecomaru, foreign matter defects were significantly reduced. This led to improvements in production efficiency and cost savings on materials.
【Product】Sanitary product parts 【Molding Machine】650t 【Previous Resin】Flame-retardant PP 【Subsequent Resin】Flame-retardant PP
Purging Compound | Defect Rate of Black Dots | |
---|---|---|
Previous Situation | Glass fiber-filled from another company | 4% |
After switching to ecomaru | ecomaruGWP | 1% |
燃料(可燃物)
Case Study 7
- We were particularly troubled by the high incidence of foreign matter defects, especially after producing POM at the start of the next week.
- Despite experimenting with various purging compounds, we were unable to achieve significant results.
POM (Polyacetal)
Customer Evaluation
Before | |||||||||
---|---|---|---|---|---|---|---|---|---|
Purging Compound Name | Usage Amount | Whether Double Washing is Performed | In case of double washing
Purging Compound Name | Defect Rate of Black Dots | |||||
Company A | 3-5% |
After | |||||||||
---|---|---|---|---|---|---|---|---|---|
Improvement of Foreign Matter Defects | Usage Amount | Whether Double Washing is Performed | In case of double washing
Purging Compound Name | Defect Rate of Black Dots | |||||
ecomaruGWS | 0.20% |
燃料(可燃物)
Case Study 8
- The machine used for PP molding throughout the year had been experiencing a large amount of foreign matter during production start-up, causing difficulties.
Customer Evaluation
- After switching to ecomaru and starting production, the defect rate was reduced to around 1%, achieving a significant improvement in yield.
- It is used as a purging compound for major cleaning during production start-up.
Customer Information | |||||||||
---|---|---|---|---|---|---|---|---|---|
Customer Name | Products Produced | Molding Machine Capacity (tons) | Previous Resin Resin | Color | Subsequent Resin Resin | Color | Issues Before Implementation | ||||
Company B | Industrial Machinery Parts | 100 | PP | Black | PE | Natural | Improvement of Foreign Matter Defects |
Before | |||||||||
---|---|---|---|---|---|---|---|---|---|
Purging Compound Name | Usage Amount | Whether Double Washing is Performed | Defect Rate of Black Dots | ||||||
Crushed Products | Unknown | None | Non-disclosed |
After | |||||||||
---|---|---|---|---|---|---|---|---|---|
Purging Compound Name | Usage Amount | Whether Double Washing is Performed | Defect Rate of Black Dots | ||||||
ecomaru GWP | 20 kg | None | 1.00% |
Case Study 9
- Previously, there was a regular increase in the number of foreign matter contaminations, which significantly reduced production efficiency.
Customer Evaluation
- After introducing ecomaru, the occurrence of foreign matter stopped, leading to improved production efficiency.
- Compared to conventional purging compounds, both cleaning time and discharge time were reduced. In particular, the cleaning time was reduced by an average of about 20%.
Customer Information | |||||||||
---|---|---|---|---|---|---|---|---|---|
Customer Name | Products Produced | Molding Machine Capacity (tons) | Previous Resin Resin | Color | Subsequent Resin Resin | Color | Issues Before Implementation | ||||
Company A | Consumer Machinery Parts and Others | 100 | PC | Black, White, etc. | PP, PA, POM | Clear, White | Improvement of Foreign Matter Defects |
Before | |||||||||
---|---|---|---|---|---|---|---|---|---|
Purging Compound Name | Usage Amount | Whether Double Washing is Performed | Defect Rate of Black Dots | ||||||
Company I (With GF) | 120 | Some available | Non-disclosed |
After | |||||||||
---|---|---|---|---|---|---|---|---|---|
Purging Compound Name | Usage Amount | Whether Double Washing is Performed | Defect Rate of Black Dots | ||||||
ecomaru GWS | 100 | Some available | Non-disclosed |
Case Study 10
- There are frequent defects caused by foreign matter contamination.
- During molding, the color of the previous material often gets mixed in, forcing us to stop production each time.
Customer Evaluation
- Although the amount of purging compound used and the frequency of cleaning (number of times) have not changed, the defect rate, which was gradually increasing previously, stabilized at a constant level after switching to the purging compound ecomaru.
- The color of the previous material no longer gets mixed in, eliminating the need to stop production. As a result, productivity has significantly improved.
Customer Information | |||||||||
---|---|---|---|---|---|---|---|---|---|
Customer Name | Products Produced | Molding Machine Capacity (tons) | Previous Resin Resin | Color | Subsequent Resin Resin | Color | |||||
Company B | Factory Equipment Parts | 220 | PBT | Black | PA | White |
Before | |||||||||
---|---|---|---|---|---|---|---|---|---|
Purging Compound Name | Usage Amount | Whether Double Washing is Performed | Defect Rate of Black Dots | ||||||
Company R (With GF) | Non-disclosed | Exists | Non-disclosed |
After | |||||||||
---|---|---|---|---|---|---|---|---|---|
Purging Compound Name | Usage Amount | Whether Double Washing is Performed | Defect Rate of Black Dots | ||||||
ecomaru GWS | Non-disclosed Same amount used as Before | Exists | Non-disclosed Significant reduction compared to Before |