Proposal for Countermeasures Against Black Dot Defects in Plastics
Reducing foreign matter and black dot defects is a crucial task in plastic molding operations. Here, we present effective methods for addressing and preventing black dots.
We humbly suggest considering the use of [ecomaru]! Traditionally, purging compounds containing GF (glass fiber) were said to be effective against foreign matter and carbides. We often hear that surfactant-type and foaming-type agents do not perform as well. If these methods fail, then decomposing and cleaning the equipment is considered the standard practice.
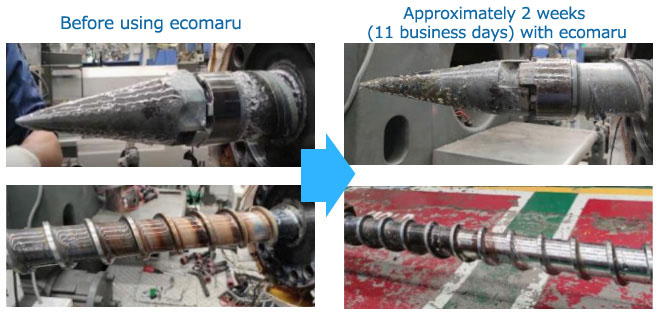
The reason we recommend [ecomaru] over GF purging compounds is that the extremely fine glass fibers in ecomaru are calculated to have 60-70 times the volume compared to a single GF fiber. This overwhelming number of fibers physically scrapes off unwanted substances. Additionally, ecomaru can reach and clean areas where GF cannot, including carbonized spots. This effectiveness allows for a reevaluation and optimization of traditional cleaning methods. Many companies are reducing costs by routinely controlling carbides.
Case
Customer Environment [Verification Conditions]
Grade: GWS Molding Machine Capacity: 650 tons Temperature: 230°C Evaluation Content: Reduction of Black Dot Defects Resin Type: HIPS
Customer Challenges
If the defect rate exceeds 10%, the machine is stopped for disassembly and cleaning. This process requires significant manpower and cleaning time, which we aim to reduce.
Effects of ecomaru
(1) First Evaluation: Carbide Removal Assessment
For two weeks (11 operating days), clean once daily with ecomaru. Verify the screw contamination before and after use and examine the defect rate trends.
Evaluation Results
Observation Conditions (Nozzle Head & Screw Body)
Before Using
ecomaru
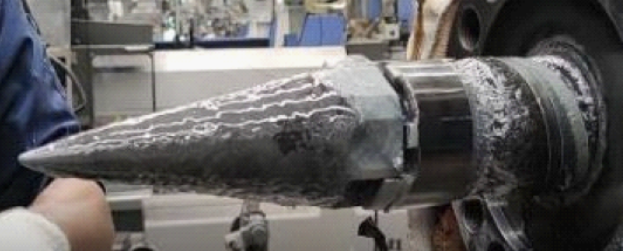
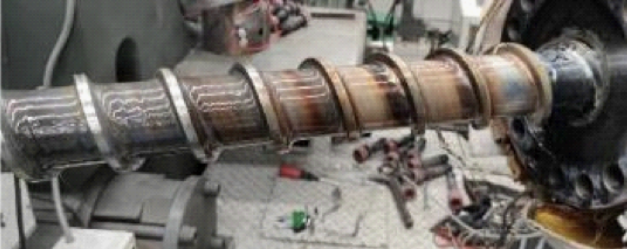
After 6 Consecutive Days of Using ecomaru
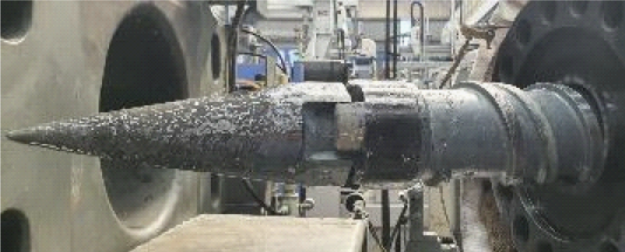
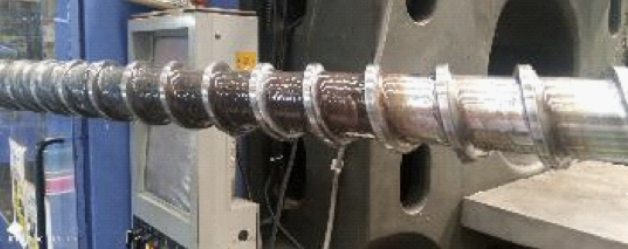
Carbides on the screw head and screw body slightly decreased.
After Approximately 2 Weeks (11 Business Days) of Using ecomaru
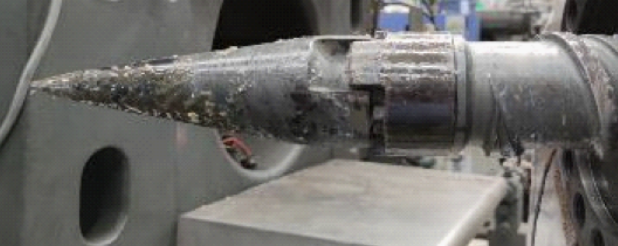
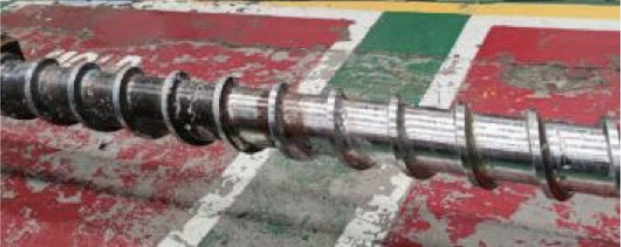
Carbides adhered to the screw head and screw body significantly decreased.
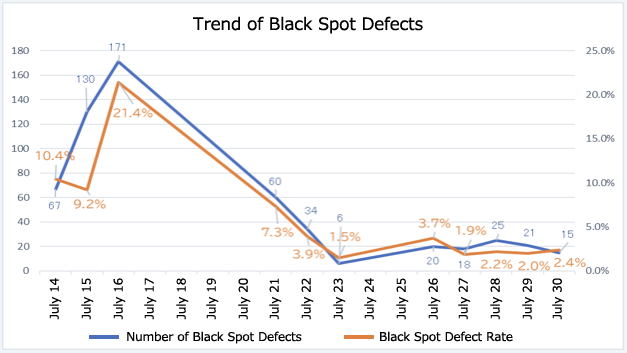
Date | Number of black dot defects | Black dot defect rate | |
---|---|---|---|
July 14 | 67 | 10.4% | Start of cleaning |
July 15 | 130 | 9.2% | - |
July 16 | 171 | 21.4% | The phenomenon of "waking a sleeping child" occurred |
July 21 | 60 | 7.3% | After the break |
July 22 | 34 | 3.9% | - |
July 23 | 6 | 1.5% | - |
July 26 | 20 | 3.7% | After the break |
July 27 | 18 | 1.9% | - |
July 28 | 25 | 2.2% | - |
July 29 | 21 | 2.0% | - |
July 30 | 15 | 2.4% | - |
[Key Points]
1. In the case of disassembly cleaning
Traditionally, right after disassembly cleaning and restarting, a large amount of foreign matter is produced, causing the defect rate to spike. Once the process stabilizes, the defect rate is reduced.
2. Cleaning results with ecomaru
Similar to the behavior during disassembly cleaning, the defect rate spiked immediately after starting the purge. Subsequently, the defect rate gradually decreased and stabilized around 2%.
As the behavior and defect rate reduction were similar to those during disassembly cleaning, it was confirmed that the cleaning effect of ecomaru can serve as an alternative to disassembly cleaning.
(2) Second Evaluation: Effectiveness in Suppressing Defect Rate
Instead of daily cleaning, investigate the optimal cleaning frequency (interval) required to maintain the defect rate around 1%.
Evaluation Results
Record of Black Dot Defect Rate
“Cleaning Once Every 2 Weeks” Interval Black Dot Defect Rate Trends
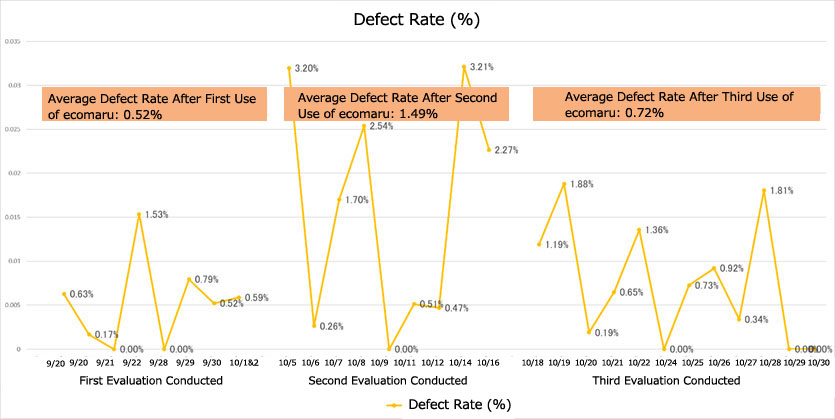
The defect rate results indicate that using GWS helps maintain the screw in a clean condition.
Evaluation 1. Two weeks after the first use of ecomaru → Average Daily Black Dot Defect Rate 【0.51%】
Evaluation 2. Two weeks after the second use of ecomaru → Average Daily Black Dot Defect Rate 【1.49%】
Evaluation 3. Two weeks after the third use of ecomaru → Average Daily Black Dot Defect Rate 【0.72%】
Summary
Before using ecomaru, the defect rate in this case was in the 10% range. By cleaning with ecomaru for approximately two weeks (11 business days), the defect rate was reduced to 2%. Subsequently, by cleaning with ecomaru once every two weeks, the defect rate was maintained around 1%, effectively suppressing it.
Many companies that are working to improve productivity and reduce the time required for disassembly cleaning have achieved positive results. Additionally, numerous companies have seen defect rate suppression and reduction effects by routinely using ecomaru instead of traditional purging compounds.
We recommend that during sample evaluation, you not only conduct a single evaluation but also verify how continuous and regular use impacts the defect rate over time. Please give it a try.
Common Causes and Countermeasures for Black Dot Defects in Plastics
Reducing foreign matter and black dot defects is a crucial task in plastic molding operations.
The main causes can be broadly classified into the following categories:
- Contamination during material feeding
- When feeding materials into the hopper, foreign matter can be introduced from the dryer or hoses.
-
Materials carbonize inside the screw
- Continuous molding causes thermal decomposition or cross-linking reactions in the resin that contacts the inner wall of the cylinder, leading to carbonization.
- After molding is completed, leaving the molding machine empty can cause the remaining resin on the cylinder and screw surfaces to oxidize and carbonize upon exposure to air.
- Flame-retardant resins and other resins that are prone to carbonization can carbonize when left stagnant or processed at temperatures higher than the recommended processing temperature.
- Adheres during mold opening and closing
These are some of the possible causes. It is necessary to take countermeasures for each cause. This time, we will focus on black dots.
Mechanism of Occurrence
1.Black Dot Formation Due to Impurities
Black dots can occur due to impurities mixed in with the plastic raw materials. This contamination can happen during storage of the raw materials, foreign matter getting mixed in during feeding, or due to poor maintenance of machinery and equipment.
2.Black Dot Formation Due to Kneaded-in Foreign Matter
When the screw is overheated, resin can stagnate, scorch, and carbonize, causing residue to stick to the screw’s wall. These scorched carbides can then mix with the molten resin and become incorporated into the molded products.
- Abnormal overheating of the heated cylinder can break the stable film, leading to the carbonization of the resin.
- As carbonization progresses and grows, it can no longer resist the flow of the resin and detaches.
- The detached areas lack a stable film and come into direct contact with the metal, leading to the formation of new carbides.
This cycle of “carbides being formed, detaching at a certain size, and causing black dots” repeats itself.
3.Black Dot Formation Due to Oxidation
Plastics can react with oxygen and oxidize. Oxidized plastic can turn black, leading to black dots. Plastics that easily react with oxygen need to be particularly monitored for oxidation.
Countermeasures to Reduce Black Dot Defects
1.When the cause is impurities mixed into the raw materials
- Purify the raw materials to remove impurities.
- Handle raw materials carefully to prevent contamination.
2.When the cause is temperature or pressure during processing, or equipment malfunction
- Set the processing temperature and pressure appropriately.
- Repair any equipment malfunctions and restore the machinery to its normal operating condition.
- Regularly clean the resin flow path and molds to remove foreign matter.
3.Disassembly Cleaning
- Disassemble the screw to remove carbides.
- While the removal of carbides is highly effective, it also removes the stable film, which may cause temporary black dot defects until the process stabilizes after restarting. This requires careful attention.
4.Cleaning with Purging Compounds
We introduce case studies demonstrating the adoption effects on our website.
Main Adoption Examples
- (1) Reduction of Black Dot Defect Rate
- (2) Eliminating the need for rinsing (double washing) to remove the molding defects caused by residual glass fibers (glass fiber) in the molding machine leads to a significant reduction in usage and setup time.
- (3) The reduction in usage and smoother replacement with subsequent resins (reduced purge volume) are achieved.