Flame-retardant resin (flame-retardant grade) is plastic material enhanced with flame retardants to increase its resistance to burning (flame-retardancy) and improve safety.
Background for the demand for flame-retardant resin
According to NITE (National Institute of Technology and Evaluation), over the three years from April 2011 to March 2014:
- Out of approximately 6,463 accident reports registered in the NITE database, 1,347 involved burning household appliances.
- Of these, 1,143 were accidents that resulted in fire spreading or personal injury.
- Among these accidents, 493 were estimated to be caused by smoke or fire originating from within the product.
Given the high occurrence of accidents due to smoke or fire originating from within products, there is a societal demand for making plastic products flame-retardant.
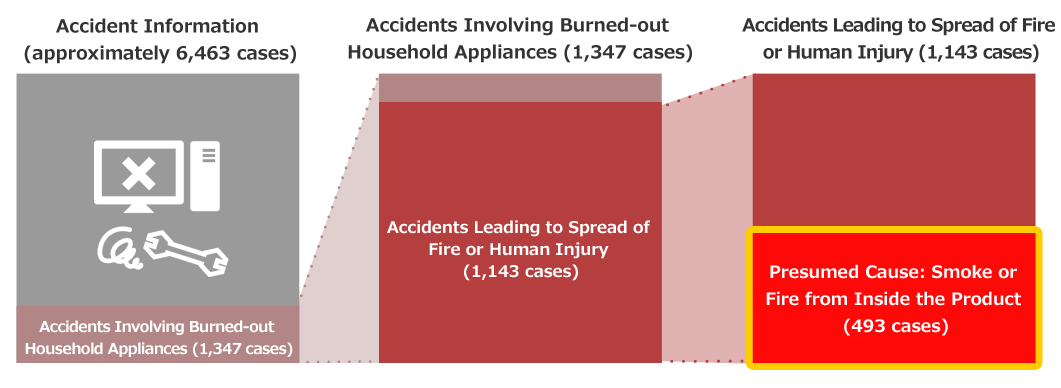
Flame retardancy of plastics
There are plastics that are completely non-combustible, known as “non-combustible materials,” and those classified as “flame-retardant materials” and “slow-burning materials” which are less likely to catch fire. For plastics to start burning and continue to burn, the following three elements are necessary.
Fuel (combustible material)
Heat (high temperature)
Oxidizing agent (oxygen)
Since combustion cannot occur without all three elements, the absence of any one will stop the burning and extinguish the fire. The purpose of adding flame retardants to plastic is to automatically block the supply of one of these three elements when the plastic ignites.
- Generate water from within the plastic to cool it
- Produce a large amount of non-combustible gas from within the plastic to lower the oxygen concentration
- Carbonize the surface of the plastic to create a barrier layer, blocking the supply of oxygen
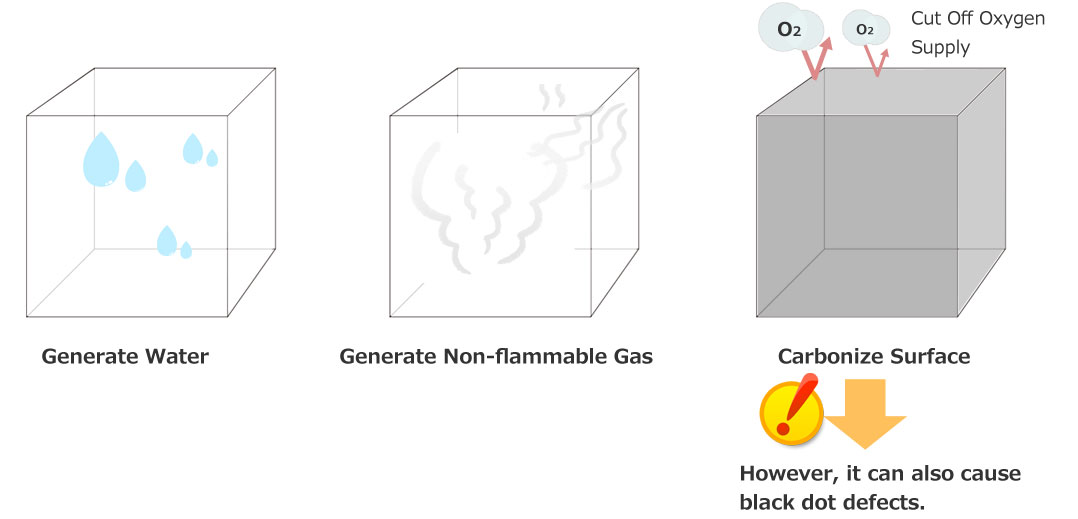
Examples of plastics that use flame retardants
Flame retardants are added to the following resins, contributing to improved flame retardancy and safety.
Thermoplastic resins | Thermosetting resins |
---|---|
ABS, polystyrene, polypropylene, polyethylene, ABS/PC alloy, saturated polyester (such as PET), modified PPE / modified PPO, polyamide (nylon 6, 66, etc.), polycarbonate (PC), super engineering plastics, PVC, etc. | Epoxy, phenolic resin, unsaturated polyester, urethane, etc. |
What is flame-retardant grade?
Flame retardant grade indicates the degree of non-flammability of plastic parts and is defined by the “UL94 standard” (established by Underwriters Laboratories: UL, a product safety certification organization in the United States). Flame retardant grade has the function of blocking the supply of any of the three elements mentioned above when plastic ignites. In particular, the function of “creating a barrier layer by carbonizing the plastic surface to block the supply of oxygen” has the very characteristic of being easily carbonized, leading to carbonization = black dot defects during molding, which is a common issue in many molding sites.
Representative materials classified into each grade
Grade | Representative Materials |
---|---|
V-0 | PEX (cross-linked polyethylene), RTV (room-temperature vulcanizing silicone rubber), PI (polyimide), PPSU (polyphenylsulfone) |
V-1 | PPO (polyphenylene oxide) |
V-2 | PA (polyamide), PC (polycarbonate) |
HB | PMMA (acrylic), PE (polyethylene), PET (polyethylene terephthalate) |
ecomaru is a high-cleaning type purging compound. It solves productivity issues in injection molding sites, such as black dot defects and poor replaceability.
Flame-retardant grade and black dot defects: Case Studies
Black dot defect rate reduced from 4% to 1%!
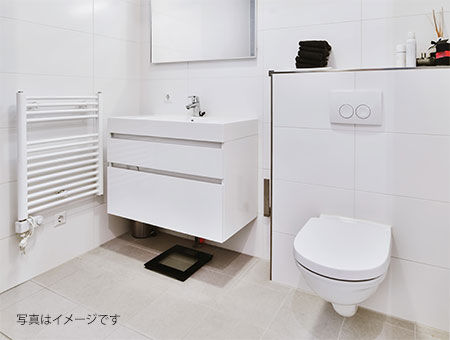
Company A: Improved defect rate
Due to the stringent defect standards for manufactured products and the large size of the molded items, the major challenges were significant production losses and cost losses when defects occurred. After switching to the purging compound ecomaru, foreign matter defects significantly decreased. This led to improved production efficiency and reduced raw material and other costs.
【Product】Sanitary product parts
【Molding machine】650t
【Previous resin】Flame-retardant PP
【Subsequent resin】Flame-retardant PP
Purging compound | Black dot defect rate | |
---|---|---|
Previous situation | Containing glass fiber from another company | 4% |
After switching to ecomaru | ecomaruGWP | 1% |
燃料(可燃物)
Improvement in production efficiency
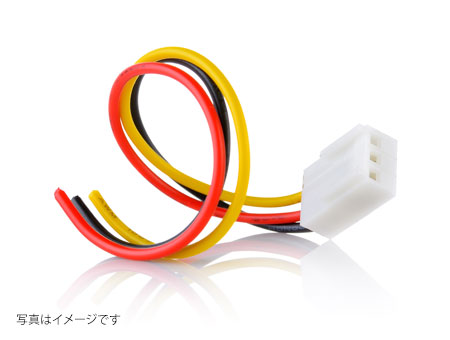
Company B: Reduction in resin change and color change time
The production of flame-retardant resin was high, and the black dot defect rate was also high, but the poor replaceability was an even greater challenge. After switching to ecomaru, the cleaning time was reduced to about half. This led to reductions in production time, usage amount, and waste.
【Product】Industrial product parts such as distribution boards
【Molding machine】100t
【Previous resin】Flame-retardant PBT (black)
【Subsequent resin】Flame-retardant PBT (transparent)
Purging compound | Purging compound usage amount | |
---|---|---|
Previous situation | No glass fiber from another company | 150–200 kg/month |
After switching to ecomaru | ecomaruGWS | 100 kg/month |